On the road: What life is like for a mobile technician
More heavy-duty repair shops are adding mobile maintenance services to their service portfolio, with four out of five respondents to Fullbay's 2024 State of Heavy-Duty Repair survey indicating they offer some form of mobile service. That's helping drive revenue for the shop and gives ambitious technicians a chance to earn more. Especially since the average mobile repair labor rate ($142/hour) was 13% higher then all labor rates, accoridng to that Fullbay study. Additionally, a third of shops said they paid their mobile techs more money, and 68% said they paid mobile techs hourly vs. 12% for flat rate/commission.
That's what the number say, but who are these technicians that brave the open road?
The first thing to know is that they can be more than just repair techs for your business.
“These technicians are not just technicians; they’re salespeople, customer service agents, billers, schedulers,” described Jordan Wagner, VP and GM of Torque by Ryder. “They’re basically running their own little business out of these trucks. Now we have the support setup to help them, but at the end of the day when they’re out in that lot, they’re making decisions based on what they feel is best.”
At a minimum, this means outfitting their trucks with the necessary equipment like relibale compressors, portable welders, and appropriate diagnostics. Torque even uses dash cams and other to ensure drivers are safe and protected in the event of a crash.
These techs need to be properly trained as well to safely perform their work, from knowing how to handle a pre-trip inspection on their own vehicle to making sure the vehicle they are working on is in a safe, stable work zone. (TMC RP 1616 has plety of best practcies to get you started.)
But it also helps to know more about what these techs workdays and nights are really like. You can't find out what that's like through any survey, so to uncover these questions, we caught up with some mobile techs to talk about life on the road.
Long hours, many miles
For many mobile technicians, early mornings and long days are the norm. For instance, Jordan Steen, owner and operator of Six Gun Diesel Performance and Repair, typically gets his Ford F-750 on the road by 7 a.m. Then, he doesn’t plan on returning home until he’s done handling construction equipment repairs for excavators, wheel loaders, and trucks.
He first began his mobile maintenance journey in 2022, and now, Steen covers a 12-county area in northwest Iowa and averages about 500 miles travelled in a week.
While a job might pop up at any time, he said things heat up after the winter thaw.
“Springs usually get pretty long when everybody tries to get going at the exact same time,” Steen explained. “It wouldn't be unheard of to have 12-hour days all spring until at least June."
Then Steen said from July to Spetember he'll pull 10-hour shifts.
Pedro Lara, the owner and a technician at San-Diego-based Diesel Integrated Solutions, runs equally long days, albeit in a more urban setting and with truck drivers as his main customers.
He ranges from from Otay Mesa on the U.S. border with Mexio to Oceanside in the north. This can mean 12 or 14-hour days starting at 5 a.m., and sometimes even getting back in the truck after he’s returned home, too.
“If they call me in the middle of the night, I’ll get up and go,” he stated. For Lara, he is most commonly called out for a check engine light, a situation that can quickly devolve into a derated engine and a driver stuck going 5 mph.
Meanwhile, the mobile technicians at KTS Enterprise, a mobile truck and trailer repair operation located in Arizona, covers a 30-mile radius from their shop.
“We have a secondary satellite shop, but we just use that for dispatch purposes for the two technicians who are more mobile than anything else,” said Sasha Spencer, KTS Enterprise operations manager. “They cover one side of the valley more and then the central location covers most of the valley.”
Staying organized
Regardless of where they roam, organization is key to every mobile repair operation. Each leveraged Fullbay’s shop maintenance platform. Steen uses it for billing, while Lara and Spencer for their service requests and records. But after that, depending on the size of their operation, each business’ organizational tactics tended to vary.
In Iowa’s backwoods, Steen uses a hand-written notebook to track his vehicle data in case he’s in an area with no cell service. Then, he uses color-coded Google Sheets to track his customers, the work their machines need, when he’s working on them and how much is left to be done, and if he needs more diagnostic information or parts.
Meanwhile, Lara and Spencer have more traditional dispatch operations, with calls scheduled on a daily basis. At KTS Enterprises, the shop manager is the one who assigns technician’s jobs the night before, depending on customer needs, preferences, and shop efficiency.
“The calendar really depends on customer needs, but I would say a technician would probably do two to three mobile appointments in a day, depending on the length of the appointments,” Spencer explained. “We do target mostly fleets, so a lot of times our appointments are for multiple units at the same appointment.”
Read more: Using mobile maintenance to proactively stay compliant
This includes assigning technician duties based on their expertise, with some focusing on preventative maintenance and Department of Transportation work, she said, while others might be qualified for more in-depth diagnostics.
However jobs are assigned, mobile technicians need to have a clear view of how they prioritize the calls that come in, whether that’s based on urgency, location, or sometimes, whether or not the customer reliably pays their bills. For Steen, if a customer is dependable at covering their costs, their job priority then depends on the level of repair needed.
“If it's a coolant leak and they've got the ability to keep it full and keep going, then maybe it doesn't have to be done today; we can get to it tomorrow,” Steen noted. “But if it's a production machine that's gotta run 10 hours a day and it's got an emissions code or it blew a turbo or something like that, then obviously that's gotta get put to the front because it's not usable as it is.”
In this way, mobile techs can be akin to field medics triaging the wounded.
“We do take priority on emergency breakdowns versus preventative maintenance,” Lara agreed, “because we know it's somebody stranded on the road against somebody parked in a yard, which can wait.”
Fighting the elements
For mobile technicians, the hurdles they faced range from the environment to regulations to everything in between. For Steen, he had to get past the mentality that whether he could fix a job or not depended on if he had the right tool. Beyond this, the sheer variety of vehicles he works on can be both a joy and a challenge.
And, of course, mother nature always has something to say about what work gets done.
“The elements are always a factor that you have to play into and know that you're not going to be going out in the backwoods and working on something after it's rained two inches,” Steen explained.
This is true for KTS’ technicians in Arizona, too, Spencer said, with heat as their main obstacle alongside occasional monsoons and haboobs, or giant dust storms.
Loadouts
Once a technician has determined which jobs must be done in a day, next comes making sure their truck has what they need before hitting the road. Steen said he doesn’t go a day without using his multimeter, so much so that he carriers a spare in his truck. He also brings his hydraulic gauges and 4” drive ratchets, taking care to keep a comprehensive set of basic hand tools close by ranging from ¼” drive sets with deep well shallows, extensions, and ratchets. Of course, a computer for diagnostics helps as well, “but it’s hard to do diagnostics without all the diagnostic equipment,” Steen admitted.
Lara tends to make sure he has larger equipment on hand and is always sure to have a welder, generator, and an air compressor, tools which broadly cover most jobs, he said.
“Then you have to have a pump and a container to carry your wasted oil and your fresh oil, because we do maintenance on that too, and basic hand tools,” Lara explained. One thing he noted has made a big difference is the shift to electric tools from pneumatic ones in the last five years.
“Several brands have come with really good electric tools for the grinders and the power tools for tightening and loosening all that stuff,” he said.
For KTS’ techs, not only are they outfitted with tablets and Fullbay’s software, but they also have multiple scanners and access to dealer-level software programs. And, of course, a reliable range of hand tools.
“I know several of the technicians are hardcore Snap-on [fans] because they have a good warranty policy,” Spencer said. “And I have heard from the technicians that when they're working on jobs, there's minimal breakage, even if a technician will run a tool through the ringer, and they still work really well.”
It’s critical that mobile technicians are equipped as well as they are, so that they’re prepared to face the challenges of the road.
But for Lara, sometimes his own equipment works against him.
“That has many challenges too, because you cannot carry all that you want on your truck because it's a heavy truck itself,” Lara said. “And then having all the parts and all the tools necessary for the job, sometimes you can’t take something.”
And his state’s work truck regulations are beginning to present problems as well.
“Downsizing the truck itself is a challenge, especially with the new rules and regulations here in California,” Lara stated. “Now, anything over 14,000 pounds needs to be certified by CARB and regulated, and it's getting trickier and trickier to have a heavy truck and go out there and carry your shop on your shoulders.”
But despite this, Lara still loves the call of the open road and his ability to help the people he meets along the way. It’s all about pacing yourself on the road ahead, day by day and job by job.
“As a technician, take it one step at a time,” he concluded. “It doesn't matter if you have 10 jobs ahead of you booked, finish the one you have in front of you and do the best and most thorough job that you can. Just take what you have in front of you and finish it.”
About the Author
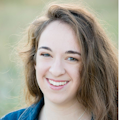
Alex Keenan
Alex Keenan is an Associate Editor for Fleet Maintenance magazine. She has written on a variety of topics for the past several years and recently joined the transportation industry, reviewing content covering technician challenges and breaking industry news. She holds a bachelor's degree in English from Colorado State University in Fort Collins, Colorado.