On bike or truck, maintenance adds up to greater efficiency
One of the activities I get to enjoy living between an east coast beach and a university is riding my bicycle in either direction, reasonably safely, using trails with low traffic roads. I ride a hybrid meaning I sit upright with straight handlebars, not to be confused with an eBike or some other assist. A typical ride will last about 90 to 180 minutes and I may make 18 to 24 miles distance.
The reason for this explanation is that it gives me lots of time to think, and on my most recent ride, I was a little more focused because of this article. I had an interesting conversation with myself about how a bike can easily scale up to a truck and how maintenance generally affects fuel economy with minimal visual change. You’ll see the connection as you read on.
Recently, I was given the keys to The Bike Medics – Mobile Shop (@thebikemedics), located in Charlotte, NC, for a few days, which was a dream come true for a bike enthusiast. There, I had the opportunity to rebuild my bike and free rein on parts and tools. The only thing missing was an experienced technician providing direction but heck, I was a truck shop “gofer” for a couple years in high school, worked as a technician in an OEM’s testing facility for a few years, and have broken (and had to repair myself) enough things since purchasing our first house in the 1970s that I should be comfortable with R&R on a simple bike. Or so I thought.
My first lesson was replacing the brake and shifter cables that are routed inside the bike frame. The second was finding out that the cables are actually different sizes! I did go through the whole bike the same as a proper tune-up technician would have done. I did spend lots of time on YouTube and it only took me about three days to do what a trained bike tech does in about two hours. But, when I got the bike home and took it for my first ride, it rode like silk—easier to pedal, no noise when I braked, and it seemed a little more solid.
My point is that when moving mechanical things move, there are unseen changes that affect the efficiency of the whole system. And it is difficult to find a tangible percentage increase for each item, but in the end, it’s worth the investment.
Fleets see maintenance as important to their operation but tend to look at it as a way of reducing downtime rather than as a way of improving fuel economy. This is one of the findings in NACFE’s Maintenance Confidence Report. Reducing downtime is a good thing and it’s fine to think of it as the primary benefit but when I said the bike was “easier to pedal” because of maintenance, I found improving (fuel) efficiency came out on top.
I increased my average bike road speed by about one mile per hour as a result of my maintenance exercise. Imagine the affect of extending the service interval of all those items—lubricants, air cleaners, cooling systems, fuel filters, electrical systems, and particulate filter—that should be addressed at the correct interval, now more than ever.
When cycling, the key is to establish a comfortable cadence and to do that here in flat country, I usually pick the highest gear on the front ring and rear gear sets. I hope that is easily related to staying in top gear if you’re a truck driver because the analogy is similar. Although chain drives for bikes haven’t changed much since the 1880s, lubricants have. There are wet (oil-based) and dry (wax-based) lubes. Dry lubes stay clean longer because they attract less dirt and dust, but they require more applications. The first application of the dry lube requires the factory grease and any other chain lube to be completely removed. Wet lubes stay liquid and are compatible with factory grease or other oils. Wet lubes stay on the chain longer and build up after a while.
A new chain drive is considered to have about 98% efficiency and if kept clean, adding lubricant actually does nothing to improve or degrade the efficiency. On a bike chain, lubricants help keep impurities (sand or dust) away from the pivots and keep those pivots from deteriorating which increases the chain’s life.
I told you I had a lot of time to think on my rides. My point is, selecting the right lubricant has a significant effect on system efficiency.
The latest engine viscosity oils (CK-4 and FA-4) have improved fuel economy 0.4% to 0.7%. It’s an easy maintenance change that can be made to the entire fleet to raise the fleet average fuel economy without too much additional investment, but the return is significant. Another interesting fact is too little or too much engine oil can create more friction and rob the engine of power, decreasing fuel economy. For example, exceeding the recommended oil level can result in oil churning and spin losses. Cummins has found that churn losses can reduce fuel economy by up to 2% in engines, but it also applies to transmissions and rear axles.
My lungs and combustion engines both need cool, clean air to operate efficiently. As air intake systems begin to become constricted, either from a dirty air cleaner, a charge air cooler, or the piping, an electronically controlled engine compensates for small restriction increases. It doesn’t take long for the engine to begin to adjust certain criteria significantly which means it will maintain the same emission-to-BHP ratio and reduce performance. This is a prime example of how a slow change over time may not be noticed but it’s occurring. And as the engine adjusts on intake side, the DPF and SCR may increase their activity on the output side placing more stress on the entire system.
Cooling systems' higher heat rejection means increased focus is needed on this system and particularly on fan drives. Smart fans are designed to fail “on” to protect the engine and run on an as-needed basis to save fuel. They’re off more often than they are on even through the higher loading cycles like while traveling a long uphill grade. When that happens, the ECM will adjust, and the driver may not notice. Fuel economy will be significantly reduced—it can lose in the 8% to 12% range. Smart air compressors are controlled similarly, and excessive air compressor operation can cause a fuel economy loss of up to 2%.
Clogged fuel filters can cause excessive heat build-up and may allow contaminants into the system. Excessive heat build-up can be serious, as it can damage the fuel pump and injector systems. Today’s diesel engines have higher fuel system operating pressures that depend on unobstructed fuel flow to help keep the pump and injectors cool, compared to trucks in the past. Both things can lead to heat build-up in the event a filter becomes clogged. Fuel systems also have much stricter tolerances than before, with the orifices in a fuel injector measured in the thousandths of an inch, meaning that the smallest amount of contamination in a fuel system can have a big impact on the fuel injectors and consequently hurt fuel efficiency.
Of course, wheel alignment, correct tire pressure and aerodynamic device maintenance go without saying. See my previous blog on the ROI of aerodynamic devices.
Profits are made while trucks are running and at times it can be a challenge to schedule equipment for optimum service intervals. Fortunately, telematics technology suppliers have continued to improve their products and can help show the advantages of earlier service rather than later service. This helps you begin saving fuel earlier in the cycle. Close monitoring practices and tweaks will help build a strong business case for a maintenance investment that might be considered marginal without accurate data. Seeing how those savings are directly related to fuel is the reason I believe fuel economy is the number one benefit of a strong maintenance program.
It is all those little maintenance items that added up to bigger savings. I could go on, but I think it’s time to lube the chain, check tire pressures, and take a ride to the beach.
About the Author
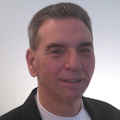
Frank Bio
Frank A. Bio, FABio Transportation Consultation founder and president, has been part of North American Council for Freight Efficiency since 2019, contributing to Confidence Report updates and various other assignments including autonomous and electric vehicles. Prior to retiring from Volvo Trucks as director of sales development – specialty vehicles and alternative fuels, Bio led Volvo’s sales force education and portfolio for alternative fuel and specialty vehicle. He also advised motor carriers considering alternative fuel vehicles and vocational trucks. Bio started his career in 1972 in the heavy-duty commercial vehicle industry, serving in a variety of positions including engineering, service, marketing, and sales.