Rush technicians share what shop practices work for them
It’s always a challenge to know how best to manage your technicians, as their wants and needs change from generation to generation and person to person. There are ways to get an idea of what the majority of techs want via surveys like the one recently released by WrenchWay, a non-profit organization that promotes the vehicle repair trade. Called the Voice of Technician (VOT) Survey Report, the annual study found that technician job satisfaction declined in 2024 versus 2023, with a large majority of diesel techs particularly unsatisfied with training, communication, and career trajectory.
But what do individual techs think about the industry? We recently had the opportunity to find out, as Rush Enterprises invited us to witness the company’s Tech Skills Rodeo, a maintenance competition held in San Antonio every December. Around a third of the national maintenance provider’s 2,800 techs were on hand, and though we didn’t want to distract them from potentially winning a great prize package (eventually won by Georgia-based technician Christopher Purcell) we did manage to discuss some pressing shop topics with 10 techs to get a better sense of what they want and why.
Here are their thoughts on their preferred work hours, pay, and their feelings about the industry.
Preferred work hours
While WrenchWay’s survey found that an equal amount of technicians preferred 10-hour days with four-day work weeks (32%) and 8-hour days with five-day work weeks (32%), at Rush, 70% of the technicians we interviewed were interested in a shorter work week with longer days, even if they didn’t usually get them.
Prior to his current posting, Shannon Smallman of Rush Truck Centres of Canada – Ottawa East had a staggered 4-day work week, with his rotation running Monday through Thursday one week and Tuesday to Friday the next.
“Every other week we'd have a four-day weekend,” Smallman commented. “And it was awesome.”
For some, such as Terry Truman and Derek Hambly from Rush’s Mississauga, Cana location, their coworkers even had 3-day work weeks with 12-hour days.
“It helps because there's no break in between—you’re working 12 hours straight instead of off and on, cleaning, putting tools away,” Hambly explained.
However, some Rush technicians noted that they might not prefer the longer days and shorter weeks because even with 5 days in the shop, they’re still working 10-12 hours a day anyway. This could potentially mean a mandated 10-hour day would stretch even longer, adding even more wear and tear to their bodies.
Read more: The Uptime Paradox: The cost of ignoring technician health
“It's usually more than eight hours a day, just to either finish a job or get ready for the next day so you don't have to go back to the previous day’s workload,” said Pieter Dezwart, of Rush Truck Centers – Doraville, GA.
Management takeaway: There’s no guarantee your techs will end up loving or hating an alternative to the typical 5-day work week, but it won’t hurt to ask them and consider testing a four- or even three-day work week if your operation can support it. At the very least, it shows you’re willing to accommodate your employees and respect their personal time. In the WrenchWay survey, only 47% of diesel techs said they felt valued and respected by management, a 9% year-over-year drop. And what manager doesn’t want their employees to respect them?
Preferred pay structure
Another important element of technician satisfaction is their pay structure, with 55% of VOT respondents saying that a better pay structure was an urgent industry issue.
And what kind of pay structure would technicians like? Thirty-six percent of auto and diesel technicians prefer hourly or salaried pay, with 25% wanting hourly pay with a production bonus and 19% wanting a flat rate with a 40-hour guarantee. For diesel technicians, the disparity is much larger, with 64% of diesel techs wanting hourly or salaried pay, and only 11% wanting any kind of flat rate pay structure.
Six of the Rush interviewees said they preferred hourly pay to flat rate. While Dezwart did say that flat-rate pay could be more profitable, once he got used to the structure and understood it, most technicians preferred the stability of hourly pay, particularly due to the added stress and expectations that come with flat-rate work.
Smallman noted that he preferred hourly pay “especially when you get the SRTs (standard repair times) that are so unbeatable that you can’t come close to them.”
In this case, flat-rate pay also isn’t as feasible for mobile technicians, a sector that Rush Enterprises has been working to grow.
Jason Wilder, Rush Enterprises COO, estimated that the company currently employs about 670 mobile technicians. But for these 670 technicians, their drive time to reach their clients may cut down on the number of vehicles they service, cutting into the money they can earn with a flat rate.
“I definitely like to have my guarantee where I know how much I’m bringing home,” agreed Jeremy “JJ” Jolly, a mobile technician based in Tyler, Texas.
Additionally, Rush technicians noted they preferred hourly pay to help tide them over during slower months. Such is the case for Robert Lavalley, a technician based out of Flagstaff, AZ.
“Usually in Flagstaff, we have some pretty harsh winters, and sometimes they close I-40, and then our business gets really slow,” Lavalley noted. “So to be on flat rate, you'd be showing up at work, standing around, pushing a broom for no pay.”
Management takeaway: Fleet techs are typically paid hourly versus flat rate, but consider incentives based on productivity and repair accuracy (no comebacks) to get your techs to hustle like a flat-rater.
Overall industry sentiment
But despite these challenges, the technicians at the Rush Technical Skills Rodeo differed from WrenchWay’s VOT survey in a key way. While WrenchWay found only 21% of diesel technicians would recommend the industry to a newcomer, at the Rush Rodeo, just about all of the technicians said they would.
“I love it,” said Jose Garza, a tech based in Pharr, South Texas. “We’ve got to keep America moving.”
Other technicians echoed Garza’s pride in their work and noted that they enjoyed the challenge of the work and the chances to always be improving, not to mention the job security that comes with turning wrenches.
After all, “a robot can’t do our jobs,” said John Egner, a technician at the Columbus, Georgia Rush location.
This doesn’t mean the technicians at Rush didn’t note that the job comes with its own challenges, and that while they’d recommend becoming a technician, that doesn’t mean it doesn’t take a special kind of person to do the work.
“It's definitely a tough job getting started and having to buy your own tools is never fun to begin with,” Jolly commented. “But I still enjoy it. And there’s good money in it if you’re not cut out for college.”
Management takeaway: Not every company has the resources to fly a third of their employees to essentially a massive team-building exercise, but there are economical ways to breed esprit de corps within your team (and we don’t mean with monthly pizza parties, as periodic company-paid lunches ranked at the bottom of technician concerns for any shop they’d work at. Instead, they rated paid time off as most important). What that is will be up to you to find, but it may revolve around letting your technicians see less of you instead of eating with you.
About the Author
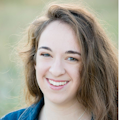
Alex Keenan
Alex Keenan is an Associate Editor for Fleet Maintenance magazine. She has written on a variety of topics for the past several years and recently joined the transportation industry, reviewing content covering technician challenges and breaking industry news. She holds a bachelor's degree in English from Colorado State University in Fort Collins, Colorado.