When tubeless radial truck tires first came on the scene decades ago, the industry gradually moved away from tube-type assemblies on multi-piece rims for multiple reasons. Besides the obvious advantage of eliminating the possibility of decapitating rim components during a separation, fleets quickly recognized that treadwear and performance improved because the assemblies ran cooler without the tube and flap generating additional heat inside the tire.
Moreover, since the one-piece rims were considerably more balanced than their multi-piece counterparts, the ride improved as well.
As technology all around the tractor continue to evolve, fleet expectations continued to rise. Back in the day, vibrations in the cab were accepted because drivers were used to the ride being rougher than the standard passenger car. But the combination of tubeless radial tires with air-ride suspensions and cabs changed everything. What was once considered the nature of the business became a problem in need of a solution.
Another unintended consequence of the tubeless radial truck revolution was the unwillingness to accept irregular treadwear. Tube-type tires were notorious for uneven wear because there were so many variables related to the rotating assembly. With many of those variables eliminated, fleets expected smooth and even treadwear regardless of the application.
NO SIMPLE MATTER
To the outside observer, tire performance should not be a problem on a single-piece rim or wheel assembly. You just mount the tire, seat the beads and inflate it to the recommended pressure. It doesn't appear to be complicated or difficult, so why is it even an issue?
In order for a tubeless radial truck tire to perform, it must be concentrically seated, or centered, on the rim, especially on steer axle positions. The slightest amount of variation can result in irregular treadwear. Hence, technicians must take the necessary steps to ensure the tire is properly seated.
Standard industry practice is to measure the distance between the edge of the rim flange and the molded rib on the lower sidewall. If that distance varies by more than 2/32 of an inch, then the tire is not centered on the rim so irregular treadwear and vibrations are likely to follow.
But knowing that the tire is not concentrically seated is only half of the battle. The key is to prevent it from happening in the first place so it never becomes an issue. Again, what appears to be a relatively simple and easy process can quickly become complicated if technicians do not follow the recommended procedures for mounting and inflation.
RIM CONDITION
Everything starts with the condition of the rim. If the bead seat area is not clean and free of corrosion, the beads of the tire can get hung up. A wire brush should be used to remove all surface debris before an approved rubber lubricant is applied to the bead seat.
While we're on the subject of approved rubber lubricants, it's equally important to select a product that will not have an adverse effect on the tire. Petroleum-based lubricants and those designed for other applications - like dishwashing soap - can lead to problems down the road if they allow the tire to slip on the rim or damage the rubber.
The same approved rubber lubricant must also be applied to the beads of the tire. It must cover the entire bead from the toe - the point where the bead meets the innerliner - to the molded ribs on the lower sidewall. Care must be taken to avoid excess lubricant inside the tire cavity as it can lead to corrosion issues on the rim surface.
Excessive moisture inside the tire can also cause long-term damage to the casing as the natural diffusion of air through the tire body oxidizes the steel body cables.
It's also important to recognize that most lubricants dry after a certain amount of time has elapsed. A common practice in the industry is to mount several tires at a time and lay them out across the floor. Once all of the tires have been mounted, the technicians begin the process of seating the beads and inflating the tires.
In most cases, the tires that are seated and inflated last will basically have no lubricant on the bead or rim surfaces so concentric seating is unlikely.
OTHER INFLUENCES
Another reason for non-concentrically seated beads is the position of the tire during the seating process. Some technicians will stand the tire up to seat the beads. This allows gravity to force the rim down so the tire is not centered. If the beads are seated while the tire is horizontal, gravity is taken out of the equation so the technician has a much better chance of centering the tire on the rim.
This is particularly important when mounting tires for the steering axle since the slightest amount of variation in the rotating assembly can lead to irregular wear patterns that often lead to ride disturbances.
Finally, it's crucial that the correct inflation pressure is used on every wheel position. The easy way is to just inflate everything to the maximum pressure molded on the sidewall. In most cases, however, that results in an overinflated tire.
While overinflation is definitely the lesser of two evils when compared to underinflation, it can still result in accelerated tire wear and increased cost per mile. The best practice is to work with the tire manufacturer to determine which inflation works best for a given application.
RESOURCE GUIDE
Tire mounting involves a lot more than just prying the beads over the rim and inflating the tire. When done properly, fleets can expect maximum performance if the assembly is maintained.
TIA's Fleet Tire OSHA Compliance Training Program covers the procedures for mounting and inflating tires so trucking companies can maximize the life of every tire, regardless of position. For more information, contact TIA's director of training Chris Marnett at 800-876-8372, ext. 106 or [email protected].
About the Author
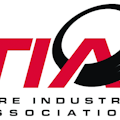
Tire Industry Association
The Tire Industry Association (TIA) is an international association representing all segments of the tire industry, including those that manufacture, repair, recycle, sell, service or use new or retreaded tires, and also those suppliers or individuals who furnish equipment, material or services to the industry. TIA was formed by the July 2002 merger of the International Tire & Rubber Association (ITRA) and the Tire Association of North America (TANA). TIA’s main office is in Bowie, MD. The association has more than 6,000 current members.