Wrench time is the amount of productive time in a day. It is the time spent actually doing PM, corrective maintenance or even fixing breakdowns. It does not include getting parts, manuals, driving to a broken down unit, jockeying units in the yard, etc.
Traditionally, wrench time was defined as time spent by the worker with tools working on the machine. It includes direct troubleshooting. By convention, we now include LOTO (lockout/tagout) and confined space entry setup as part of wrench time.
How long does it take to repair a tire or replace a pump seal? If you were thinking of the pure work time and assumed everything needed was right there in front of you, then you would be thinking of wrench time. But if you were thinking of the time from when the job is handed out to when the worker is available for the next job, then you are thinking of work order time.
Wrench Time and Work Orders
There is the misconception that wrench time can be gotten from the work order system.
Actually, there is no way to derive wrench time from work orders. The reason is that the work order is at best an approximate document. Minor (and some major) non-work activities are just not recorded.
Of course, you can estimate wrench time by multiplying the work order time by 33 percent, but the lack of granularity minimizes the usefulness.
Why is this important? Because all your productive maintenance and repair activity come from your wrench time. Obviously, if you have enough people for all your workload and projects then wrench time is of lesser importance. But if you struggle to meet all your demands, then the wrench time becomes urgently important.
Non-Wrench Time
Another way of thinking of the non-wrench time is to think of friction. A certain amount of friction is needed to make things work. A certain amount of set-up time is needed to do maintenance. But an excessive amount of friction soaks up the energy until eventually no useful work is done.
Studies done a while ago, before LOTO rules were put into place, show that a typical maintenance technician or electrician only spends around 168 minutes of a 480-minute day doing maintenance work - called wrench time.
The most popular study shows:
Activity |
Percentage and minutes per day |
|
Receiving instructions |
5% |
24 |
Obtaining tools and materials |
12% |
58 |
Travel to and from job (both with and without tools and materials) |
15% |
72 |
Coordination delays |
8% |
38 |
Idle at job site |
5% |
24 |
Late starts and early quits |
5% |
24 |
Authorized breaks and relief |
10% |
48 |
Excess personal time (extra breaks, phone calls, smoke breaks, slow return from lunch and breaks, etc.) |
5% |
24 |
Direct actual work accomplished (as a percentage of the whole day) |
35% |
168 |
Accurate Wrench Time
There are two ways to obtain accurate wrench time. The hard way is to position yourself so you can see most of the workers and assign someone to observe and have them tabulate how much time is spent doing what. The easy way is to use work sampling.
A simple way to understand work sampling is to imagine taking randomly timed snapshots of the whole shop floor wherever anyone would be working, then tabulating those random snapshots into a table of checkmarks per activity. Once you have enough observations, you can determine the number of observations needed to determine wrench time.
A handy way to make this determination is to use the graph located at http://work-sample.com/nomograph.html.
To learn the basics of work sampling, the same website has a work sampling game, located at http://work-sample.com/work-sampling-game.html. You observe the technicians fixing cars in a repair shop and at random times (dictated by the game) you have to record your observations.
The objective is to match the computer's observations. Along the way you can learn how to conduct work sampling.
But the real question is "why bother?"
Remove Barriers to Improvement
If you remove the barriers the wrench time will improve. The barriers to improved wrench time include everything from inefficient storeroom systems to slow permitting to inadequate coverage by certain crafts. Use work sampling to discover where lost time is hiding.
One of the great contributions of the Lean Maintenance crowd was to take your wasted time and see if an intervention would reduce the waste. The process is to make what is called a Pareto chart where the losses are listed by the size. This information can be used to brainstorm ways of reducing the wasted time, hopefully without unintended consequences.
In the next column, I will discuss some of the wasted time that was found by work sampling and what could be done to improve the wrench time.
About the Author
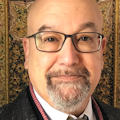
Joel Levitt
President, Springfield Resources
Joel Levitt has trained more than 17,000 maintenance leaders from more than 3,000 organizations in 24 countries. He is the president of Springfield Resources, a management consulting firm that services a variety of clients on a wide range of maintenance issues www.maintenancetraining.com. He is also the designer of Laser-Focused Training, a flexible training program that provides specific targeted training on your schedule, online to one to 250 people in maintenance management, asset management and reliability.