Devising a comprehensive system for efficiently managing parts and shop inventory is an important element to asset management. It is also a struggle. While maintenance managers are experts in vehicle service, they usually aren't as proficient in inventory management.
Too much or too little inventory is never good, and finding that middle ground seems next to impossible. If the right parts are not on hand when needed for vehicle maintenance or repairs, downtime is prolonged and that adds costs.
Maintenance facilities have invested in equipment, tools and highly qualified technicians with the sole purpose of ensuring vehicles remain on the road, says Michael Mallory, president of AutoPower Corporation, a company that provides tailored-to-fit integrated warehouse distribution business systems. Planned or unexpected downtime interrupts anticipated fleet performance. So do shop activities, scheduling, available resources and lack of adequate inventory, because these all have a way of causing unacceptable downtime.
When it comes to managing parts, there are several key objectives, Mallory says. One is to have the right inventory mix for the vehicles in the fleet. That helps ensure less time in the shop and more time on the road.
Another objective is to have a profile of parts required for the scheduled maintenance events. This will provide quicker turn around of vehicles, he says. Knowing planned upcoming PM schedules gives adequate time for having the required parts in stock.
EMERGING TECHNOLOGY
Parts management has evolved over time. Now, there are numerous ways and methods to cost-effectively and efficiently manage inventories, predominately by embracing technology through computer and inventory software. Without technology, inventory control is done through manual means or by experience and guesswork, and those are not good methods for operating a shop, especially in today's demanding and competitive environment.
Typically, maintenance shops devote too little time to proper stock planning, observes Mallory. "Computerized inventory procedures can go a long way with maintaining proper inventory levels." Beyond that, "shops utilizing specially designed software for managing shop operations are better able to limit the unexpected."
There are multiple benefits and advantages of using computer programs for managing parts, and they vary widely by application, says Troy Wruck of PMXpert Software, a leader in providing CMMS (Computerized Maintenance Management Systems). Overall, he says, these programs ultimately add to a company's bottom line by increasing shop and vehicle productivity. By ensuring the appropriate parts are available when needed, day-to-day costs and equipment downtime are reduced.
"The number one benefit of automated parts inventory systems is that its ROI is normally less than six months and the savings thereafter go directly to the bottom line at no expense, adds Charles Arsenault, CEO of Arsenault Associates, an innovator in the field of fleet asset maintenance management software and technologies. Moreover, the systems significantly increase inventory accountability and help with development of annual parts spending budgets.
There is also increased parts accuracy from elimination of duplicate part numbers, says Dave Walters, technical sales manager, TMW Systems, a developer of enterprise management software for the surface transportation services industry, including logistics, trucking and heavy duty repair and maintenance. Some systems have ability to track usage history and recommend correct stock levels, as well as handle inventory replenishment based upon usage. There are also systems that can track vendor charges and provide cost controls, and track aftermarket parts warranty, he says.
Furthermore, with computer and inventory management software, "entering and looking up data takes less time than doing it manually on paper and using file cabinets," notes Bill Ashburn, vice president, Prophesy Transportation Solutions, a provider of software solutions for the trucking industry and an Accellos Company. Adding barcoding can speed accurate data entry and locating parts and, "electronic data storage uses less paper."
Systems can track parts history to identify faulty parts and perform comparative analyses between different manufacturers in order to purchase the highest quality and most cost-effective parts, he says. This enables better control of vendor spending and pricing.
"Parts purchasing for planned stock replenishment ensures keeping inventory at optimal levels," says AutoPower Corporation's Mallory. "For multi-shop fleets, being able to ‘see' the available stock in the other shops can often prevent purchasing the out-of-stock item, but rather transfer the part.
"With shop quotes maintained in the computer, out-of-stock conditions can be avoided when testing the quote's stock requirements against the inventory levels. Then, parts purchases, transfers or even special orders can be completed in advance of the vehicle arriving for service. Smart software can easily keep track of these stocking demands on a daily basis and have alerts broadcast when stocking conditions warrant the attention of the buyer."
Moreover, there are systems that begin tracking warranty once an item is installed on a unit, says TMW Systems' Walters. Inventory levels can be monitored and stock quantities are adjusted based upon usage, history, seasonality and procurement time. Inventory and purchasing data can flow seamlessly though automated interfaces to a company's business accounting system, improving data accuracy and reducing staffing requirements.
Beyond that, there are computerized systems that can manage cores and disposals and associated costs, and control defects, exchanges and returns, Ashburn of Prophesy Transportation Solutions adds. They can also and keep track of multiple cost levels and automatically use the correct part based on the FIFO (first in, first out) or LIFO (last in, first out) methods, as well as automatically assign part markups by customer or globally.
SPEEDING WORK
Proficient inventory management provides an organized work environment, PMXpert Software's Wruck says. "Knowing what parts are in stock, when to reorder, which assets are going to be serviced in the upcoming weeks and having access to historical costs allows shops to run smoothly with effective time management, reducing parts costs and wasted labor."
When parts are available when needed, technicians can complete repair work in an efficient manner and return the asset to service, adds Walters of TMW Systems. At the same time, inventory controls maintain the correct stock levels to accomplish this task while preventing and eliminating over stock situations. The result is improved technician efficiency and streamlined work bay productivity.
"Having the correct part available when needed eliminates excessive downtime, Arsenault Associates' Arsenault agrees. "It is not unusual to see a $100,000 vehicle out of service for a $10 part.
"Without an effective parts inventory process, preferably software, the fleet maintenance department will have to spend an inordinate amount of unproductive time managing their parts," he goes on. "Parts, tires, batteries and even fluids all need to be managed carefully, and a manual system is just unproductive, and in many cases unsustainable, due to the manpower it takes to manage it correctly.
"The other thing we've seen is that because inventory management is time consuming, some under-staffed fleets will have a tendency to lean too heavily on their part vendors for the management of their inventory. This is like letting the fox watch over the hen house."
Adds AutoPower Corporation's Mallory: "Having the stock ready when the vehicle rolls into the service bay, limits downtime, eliminates costly emergency parts orders and keeps technicians working. Since most fleet shops are a cost center, cost reduction continues to be management's ongoing mantra for impacting bottom line results" and inventory management systems can help fleets achieve this."
ADDING PERFORMANCE
Greater benefit and cost saving can be gotten with an inventory management system that is part, of or used in combination with, a fleet or maintenance management system, Arsenault points out.
PMXpert Software's Wruck says there are CMMS that can manage both pre-scheduled preventive maintenance and on-demand maintenance and tie in seamlessly with automated inventory management processes. For example, systems can, upon creation of a work order, flag the required parts and reassigns them from an "available" to a "needed" status. The parts are automatically "pulled" out of inventory when the work order is closed and confirmation is given that the parts were used.
CMMS can also send an e-mail notification to the purchaser to flag that parts are needed when those parts fall below a pre-determined desired quantity available, says Wruck, and then automatically create a purchase order or purchase requisition.
There are systems that are an integrated suite of products for managing every part of a transportation operation, notes Ashburn of Prophesy Transportation Solutions. They have modules for dispatching, accounting, mobile communications, commercial mileage and routing, fuel tax reporting, fleet maintenance, parts management, driver log auditing, driver management, logistics management and more.
"These modules are typically fully integrated and share common data so that users never have to enter data twice, as all of their critical information flows in real time throughout every part of their business," he says.
IMPLEMENTING SYSTEMS
"If you're going to deploy a parts inventory management system, make sure it is part of, or can be integrated with, your fleet management system," advices Arsenault of Arsenault Associates. "Identify whether you will need to upgrade your company's existing technology or infrastructure to effectively use the software," adds Ashburn. "Is a new or upgraded network, server or other computer hardware needed? Will any staff changes be needed?" The objective, he says, "is to purchase the best possible system - the one with the features and capabilities you actually use - that is in your budget."
"Use of technology like barcoding to identify and document parts onto a repair order should be considered a necessary feature today," Arsenault says. "Hand-held computers with barcode scanning capabilities are well within the cost range of any shop and the amount of productivity they provide far out paces their cost."
"Make the right investment in your system," he stresses. "Don't do it on the cheap or piece meal the process as in the long run the costs and disturbance to your shop operation will be considerably more."
Because there are so many capable software products available, choosing the right one requires an investment in time and effort, says Mallory of AutoPower Corporation. "Mistakes in selecting software that doesn't fit your shop is much more costly than just the price of the software."
PURCHASING POINTS
There are a number of key considerations when looking to buy or upgrade a computerized inventory management system, aside from cost and ROI, agree all of the company representatives, who say some fundamental question must be answered before looking for software. At the top of the list: determine the specific needs, requirements and functionalities of the system that are "must have" and "would like to have," and decide if it will be a stand-alone or networked program.
Consider usability and scalability, Ashburn says. "Is the software intuitive and easy to use? Features become meaningless if you can't effectively use them. If your company grows, can the software grow with it? Can you add more users and more features as needed? How much training will be needed for your staff?"
Other important considerations, the company officials concur, are: the underlying quality of the software; frequency of program updates; ongoing after-sale support plan; getting references of companies about the size of your operation who are using the software being considered; and checking the financial condition of the program's provider to insure it will in business for the long run.
In addition, AutoPower Corporation's Mallory suggests determining: was the software designed specifically for vehicle service shops; can the software link to the manufacturer's website for technical information; and does the software provider provide training, and if so, what type of training - DVDs, manuals, web training, face-to-face training, etc.?
Go over all the information gathered and narrow the list of vendors down to say the top five.
TEST DRIVES
All of the company representatives suggest taking computerized inventory control programs and systems for a "spin" to get a feel for how they function.
"Software demonstrations are a good way to demonstrate the functional tools of a software solution," says TMW Systems' Walters. "Demonstrations should not only focus on the tool set available, but also on the benefits that will be achieved through proper implementation."
"Make sure the software will meet your needs during the demo," says Prophesy Transportation Solutions' Ashburn. "Ask questions ask specifically for demonstrations of the features that will fulfill your needs."
PMXpert Software Wruck's notes that obtaining software demonstrations is easier now than ever before. With web conferencing and online meeting services, "vendors can connect their computers to yours - and all of your colleagues - to demonstrate their applications over the Internet and from the comfort of your own computer station. No longer is there a need to incur time-consuming travel expenses as online demonstrations, which typically take about one hour, can be scheduled at your own convenience with very little advance notice.
"A proper software demonstration, from a legitimate software provider, is not and never should be a sales pitch from a sales person," emphasizes Wruck. "Instead, they are a two-way communication tool and an opportunity for the software provider to illustrate the application's features and functionality, and to gain a deeper understanding of your needs.
"Software trials are equally important and are especially effective after a software demonstration has been performed," he continues. "The demonstration appointment should also double as an entry-level training session, providing you with a basic level of understanding such that you should be able to navigate the product.
"Software trials help you gain a deeper understanding of how each software application works, whether or not they have the features you require and just how user-friendly they are in comparison to one another when considering multiple options."
Following the demos and trials, measure the programs against your considerations checklist, says Arsenault. Request proposals with costs and implementation processes/timetables, carefully evaluate all proposals, then make the selection.
TAKING CONTROL
"Less inventory is not better than having the correct amount of the correct parts on hand," Arsenault of Arsenault Associates concludes. "If you are not in control, someone else is, and your costs are out of control. Attain and deploy your parts inventory software once and let it do its job so you can focus on more important issues and exceptions."
"Overall vehicle cost of ownership is simply the accumulation of the shop labor and parts used to keep the vehicle in operation," adds Mallory of AutoPower Corporation. "Managing the repair and service cost during the life of the vehicle gives management the opportunity to decide when the vehicle should be retired. At some point it becomes more economical to trade-in the vehicle than to continue sinking additional repair cost into it.
"Using computer-based scheduling, service bay assignments, technician allocation and proper inventory levels can keep shops operating at higher efficiency with optimal labor cost utilization," he points out. "What's more, computerized inventory management, preferred part's sources, contracted part prices and generous core return privileges will quickly produce a more productive shop department."
About the Author
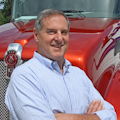