One of the nation's leading flatbed trucking companies, Melton Truck Lines offers full North American coverage, including through-trailer service to and from Mexico, a pioneering move it began in 1980. With a fleet of 800 tractors and 1,300 air-ride trailers, it has earned a reputation for consistent, on-time transportation service by proactively improving its fleet management and maintenance practices.
One of the fleet's most recent challenges has been extending out the trade cycles on its tractors, predominately T600 and T660 Kenworths - all company owned and operated. It used to sell or trade its tractors after 36 or 42 months. But with the decline in the trucking industry and the nation's economy, the Tulsa, OK-headquartered company is holding onto its equipment longer.
Melton Truck Lines buys new tractors and gets them with an extended warranty for 500,000 miles. However, it trades them after about 300,000 to 350,000 miles in order to reduce maintenance and repair costs and get a higher resale value, says Jeff Robinson, senior vice president of maintenance. All that is changing as the company lengthens equipment life cycles. That, in turn, is causing a change in the company's maintenance practices, with a shift to predictive maintenance.
"We're looking at what our most common breakdowns and repairs are to see what we need to do to preempt these things and get the trucks to live longer," he explains. "Do we need to put a clutch in, redo the air conditioning system - that type of thing. Basically, we want to figure out how to make a truck trouble free for six years or 600,000 miles."
The average age of the trailers, mostly Utility models with some Great Danes, is now 3.5 years. The trade cycle was 7 years but that lengthened to 10 years, says Robinson. "With proper maintenance a 10-year old flatbed trailer works, and as important, looks good to our customers."
KEEPING TRACK
Melton Truck Lines was founded in Crossett, AR, in 1954 by Bert and Gladys Melton to haul lumber and roofing materials in Arkansas, Missouri, Texas, Oklahoma and New Mexico. It has plenty of historical truck operation and maintenance data which is used to continually revamp the company's maintenance strategy, procedures and processes.
For many years now, it has been using maintenance management software from Innovative Maintenance Systems to help track and manage fleet inventory, preventive maintenance, repairs, fuel, parts and more. One of the nice features of the software, says Robinson, is that it keeps track of maintenance activities and can generate preventive maintenance and repair histories. Having historical information helps with analyzing costs, monitoring trends and watching the effectiveness of the overall maintenance operation.
"We're always keeping an eye on maintenance trends, looking for any spikes - for example, an increase in tire wear. When we spot one, we dig down to find out what's going on and then come up with a fix."
PUSHING PRODUCTIVITY
Any vehicle repair that "is big, major and time-consuming" is done by truck and engine dealers, Robinson says. "The job of our technicians is to get all the trucks that come through our terminals inspected, maintained and back out on the road as quickly as possible. If I tie a tech up on a job that's two days long, say, that's four or five trucks each day that can't be inspected.
"Our technicians can do it all," he notes. He prefers technicians with broad skills rather than specialties because "it makes them more flexible in what they can do, and that helps increase shop productivity." So does tracking and benchmarking technician and shop productivity, which he began about three years ago. "This helps determine how efficient our shops are operating and if there are any issues or problems." The information is also helpful when the company does the annual review of each technician.
The productivity results for all shops are posted quarterly. "Our technicians like to be challenged, and by doing this we create some friendly competition between the shops to see who can be the best."
Along with its terminal in Tulsa, Melton Truck Lines operates terminals in Dallas, El Paso and Laredo, TX; Birmingham, AL; and Youngstown, OH. While each has a vehicle maintenance operation, the largest is at the Tulsa terminal - 12 bays and 15 technicians, followed by the Laredo shop with 8 bays and also 15 technicians. The maintenance department, overseen by Robinson since he joined the company in October 2001, is made up of 50 people.
Laredo is has the biggest maintenance operation because 25 percent of the company's business is in and out of Mexico. The rigs stop there to be inspected before crossing the border. Both Tulsa and Laredo have a dedicated drive-through inspection building.
CUSTOMIZING METHODS
Melton Truck Lines uses the vehicle manufacturer's PM guidelines as a foundation for its maintenance procedures but adds additional steps developed over time specific to its operation. "We constantly track our maintenance work and costs, regularly review everything and then adjust as necessary," says Robinson.
Another way the company works to minimize unscheduled downtime is through its technicians. "We have good technicians that really stay on top of our equipment by looking for the small problems. When they find something, or see a trend developing, they deal with it and bring it to our attention. That helps us prevent the little things from developing into big problems. We want things fixed in the shop, not have a breakdown on the road."
Robinson has been in involved in vehicle maintenance since graduating from Oklahoma State University with a degree in diesel and heavy equipment mechanics in 1977. He says that "when I see a big problem develop, I use my contacts and networking to learn if other fleets have had the same or similar issues. It's good to compare and share information."
For those occasions when there is a breakdown, Melton Truck Lines has a Road Service Department. It has contracts with service providers nationwide and helps manage the breakdowns to get trucks up and running as rapidly as possible. This department is staffed by four people and operates around the clock.
To bolster its efforts to catch problems before they cause an on-road issue, about six months ago, Melton Truck Lines began a pre-trip inspection contest for drivers. The idea, says Robinson, is to help drivers improve their inspection skills and make them aware of safety issues. A rig is set up with 10 or 12 "defects" and drivers are challenged to find them.
Good pre-trip inspections are going to take on even greater importance with the implementation of Federal Motor Carrier Safety Administration's new major proactive safety program - Comprehensive Safety Analysis 2010, he notes. The program makes drivers more accountable for the condition of their vehicles.
MANAGING COSTS
Robinson says the company's stringent driver employment standards and driver training and safety programs also help the fleet keep maintenance costs under control. "We operate good quality trucks with first-rate professional drivers that care about the equipment. That results in fewer repairs and breakdowns."
Another focus has been squeezing more miles out of every gallon fuel. "That's a lot more difficult for a flatbed fleet and than a van operation," he remarks.
In the endeavor to lower fuel costs, Melton Truck Lines established a Fuel Conservation Department to focus on fuel conservation through new technologies, techniques and education. Plus, it joined the U.S. EPA's SmartWay Transport Partnership - a program that encourages freight transportation companies to be more fuel-efficient and to run cleaner for the environment.
From these moves, the company altered its tractors specs, switching from Caterpillar diesel engines with a 13-speed overdrive transmission to a 430-horsepower Cummins diesel with a 10-speed direct drive Eaton Fuller transmission. "This has made a big difference in optimizing fuel mileage," Robinson says.
It also switched to wide-base tires on its tractors. "We haven't seen a huge mpg difference, but it saves us weight, and as a flatbed operation we're real conscious about weight. And we're getting good tire life." The fleet is considering using wide-base tires for its trailers as well.
About 60 percent of Melton Truck Lines tractors are outfitted with a Carrier Transicold APU (auxiliary power unit) to allow heating and cooling of the cab without the need to run the engine. This reduces fuel use, wear on the engine and other related mechanical components and diesel emissions, says Robinson. The top considerations in the choice of APU "were the service network, because we run all over North America, and reliability."
REMOVING WIRES
Among the technologies being used to increase fleet efficiency and uptime are systems from Qualcomm, a next generation mobile technologies company. In addition to streamlining communications, tracking and dispatch, Qualcomm systems are being used to monitor, in real time, vehicle and driver performance to more effectively manage fuel consumption, safety and productivity, says Robinson. "By identifying critical performance issues that impact these areas, we can be more proactive and efficient in getting faster results."
The fleet also pays bonuses to drivers who meet certain fuel consumption targets.
Melton Truck Lines' Qualcomm systems can send e-mail alerts for certain vehicle conditions, says Robinson. For example, if there is a hard braking incident, an e-mail alert is automatically sent in real time to the safety department which will look into the matter.
Technology is also helping further the fleet's commitment to safety, Robinson notes. All new tractors are being equipped with the Iteris lane departure warning system. It is a small, integrated unit consisting of a camera, onboard computer, image recognition software and proprietary algorithms that detects when a vehicle begins to drift from its lane. When this occurs, the unit automatically emits a distinctive "rumble strip" sound - alerting the driver to make a correction.
Melton Truck Lines PMs its trucks every 35,000 miles. Only the Laredo and Tulsa terminals are equipped to do this work. But because the fleet runs very few regular routes, trying to get its rigs into either one of those locations results in too many out-of-route miles, making it costly and time consuming.
Consequently, it has PM packages set up with Petro, Speedco and TravelCenters of America. About 60 percent of all PMs are done at these facilities, says Robinson. Drivers are alerted to the need for a PM via a message over the Qualcomm at about 32,000 miles.
STABILIZING TECHNICIANS
Melton Truck Lines' operation is also benefitting from a stable technician workforce. "We have very low turnover," says Robinson. There is an effective hiring process that screens candidates for a broad background in vehicle repair and maintenance, good work history, ASE certifications and other training, among other things.
It recruits from area voctech schools and has a shadowing program wherein new technicians work with veteran technicians. Once onboard, technicians receive continuous training. "That's really important," he points out, "because things are changing so rapidly." Plus, it helps create loyalty.
"Maintenance truly is one of the critical elements to the success of Melton Truck Lines," concludes Robinson. "We devote a lot of time and resources to maintaining a sharp-looking, quality fleet.
"We want to present a good image and provide excellent performance. You can't do that with trucks that are constantly breaking down or are always in the shop. That causes frustrated drivers and mechanics, hurts productivity and loses customers."
About the Author
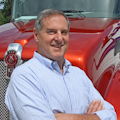