The design, layout and organization of a vehicle maintenance shop are very important. Shops ought to be set up in a way that allows for maximum functionality, safe and ergonomic working conditions and overall productivity, plus includes any environmental initiatives.
The first, and most critical, step in creating or redesigning a shop is the planning phase, says Don Leidy, principal of Maintenance Design Group, LLC. This encompasses asking probing questions and doing research.
A Denver, CO-based specialty consulting firm, Maintenance Design Group assists owners, architects, engineers and other professionals with the planning and design of transit, public works, utility, school, private and governmental operating and maintenance facilities. It is recognized as one of the leading firms in the United States in the planning and design of operations and maintenance facilities.
Understanding the shop’s current and future needs is crucial in designing the ideal maintenance facility, Leidy says. The reasons for new construction or remodeling are as varied as the individual maintenance facilities. Downsizing or increasing services, the passage of new laws and regulations, the introduction of alternative fuels and company-established green policies can all necessitate change.
Management’s expectations and requirements for a new or remodeled facility are also key, according to Leidy. Management’s vision of the new facility will shape the final design.
“A facility in southern California will have different needs than a facility in upstate New York, so each shop ends up being highly personalized, Leidy notes. “No two facilities will work the same way.”
Those involved with the design of a shop need to do their homework, stresses Leidy, who has worked on more than 500 maintenance facility projects since1976 when he started working at RTD, the public transportation agency in Denver.
The people on the project are some of the most important people on the design team and must be able to see the big picture, he says. They should visit other shop facilities and talk to other fleet and shop managers. They also should keep staff members and any other concerned parties informed and find out what their expectations are for the facility.
Good planning early on is essential to having a successful design project that comes in on budget. Equipment selection, shop layout, utility requirements, paints and finishes, etc., all need to be considered early on in the process, explains Leidy. “The earlier in the design process innovative and sustainable concepts are identified, the more likely they will be accepted as an integral part of the design.”
“After construction has begun, additions will require a change order, and change orders are expensive. A compressed air line included as an integral part of design may cost $200. During construction, the same air line could cost as much as $1,000.”
STAKEHOLDER BUY-IN
The second step in designing a new or renovated maintenance shop is building consensus, as this can make or break a project, notes Leidy. Managers should get the stakeholder group, everyone who has an interest in the project, involved in the planning and design process - whether it’s the staff, a board of supervisors, county commissioners, council members or the public. “Including everyone in the planning meetings not only educates key players about the process, but encourages buy-in or acceptance of the new facility,” he advises.
By way of example, Leidy points to the design and building of a maintenance facility in Aspen, CO, that Maintenance Design Group was involved with. “The neighborhood surrounding the project site consisted of multi-million-dollar homes, and the home owners were very concerned about the aesthetics of the project,” he recalls. “To put their concerns at ease, we invited the public to attend all design review meetings. They were included in the entire planning process.
“When we began planning this project, construction prices were flat. However, it took more than two years to get the project designed and the bond referendum passed. When we were ready to break ground, Aspen was enjoying a building boom, and construction costs had risen 40 percent - so had our budget. Because we had included elected officials and the public in the process, everyone felt like they had a vested interest in the project. They came together to help scale back the building design while still meeting everyone’s expectations.”
COMMON MISTAKES
Planning and attention to the smallest detail can prevent mistakes that can hinder the efficiency of a maintenance facility. Leidy says the following are some of the most common mistakes that create problems for shop and fleet managers down the road:
- Lighting. “It’s important to choose lighting fixtures that offer a full spectrum of light. Lighting has ramifications on the energy efficiency, functionality and safety of the facility, as well as on the general atmosphere of the workplace. For example, high-pressure sodium lights work well outdoors but aren’t suited for a maintenance shop. Inside a building, the light’s orange-yellow cast creates poor color rendition, making different colored wires look the same and blood indistinguishable from grease.
- Overhead clearance. “Ductwork, plumbing and cranes installed too low can encroach on necessary overhead space and interfere with the required unobstructed vertical clearance in the repair bay, rendering cranes and lifts useless.”
- Door size. Measure each vehicle’s width and height - including mirrors and vertical extensions, recommends Leidy. “You might think that ten-foot-wide garage doors can accommodate a truck that is eight feet wide. Most trucks usually have mirrors that protrude up to a foot on each side, which shrinks clearance from two feet to only a few inches.”
- Building finishes/aesthetics. “The bottom four to six feet of the shop walls should be durable (concrete or masonry) to withstand the abuse in a shop environment. Make sure the entire inside of the building (walls and structure) is painted to allow proper building maintenance to extend the useful life of the facility. Designing the facility’s exterior to complement the surrounding environment and adding native landscaping can help gain public approval of the project.
- Expandability. The building should not only handle the shop’s current work load, but also should be adaptable and able to accommodate demands 20 years from now, says Leidy. For example, if additional bays aren’t built during initial construction, room should be left on the site to accommodate the expansion. Also, load bearing walls should be avoided to maximize flexibility for future modifications.
- Public involvement. “Everyone who has an interest in the project needs to be informed. The best-designed project won’t get built if it’s not approved because an elected official or the public doesn’t understand the importance of the facility.”
- Appearance. “Form follows function. It’s always possible to make a functional building look good, but it isn’t always possible to make a good looking building functional.”
Maintenance shop design should also incorporate features and functions to maximize shop efficiencies, as well as technician productivity and safety.
With environmentally responsibility on everyone’s mind these days, shop greening should also be a consideration. Most sustainable design practices also make good business sense. This might include waste oil heaters, wash water recycling, water reducing fixtures, occupancy sensor lighting systems, tank-less water heaters, solar panels, using recycled materials for construction of the facility itself, and complying with LEED building standards.
The United States Green Building Council (USGBC) created the LEED (Leadership in Energy and Environmental Design) rating system to measure and certify the design and construction of sustainable building projects.
LEED is an internationally recognized green building certification system, providing third-party verification that a building or community was designed and built using strategies aimed at improving performance across all the metrics that matter most: stormwater management, energy savings, water efficiency, CO2 emissions reduction, improved indoor environmental quality and stewardship of resources with sensitivity to their impacts.
CHARRETTE APPROACH
Maintenance Design Group uses the Charrette approach when designing a maintenance facility. This type of approach is an intensive, on-site planning and design session that brings people from different disciplines and backgrounds together to explore design options.
“It accomplishes in one week what can take months if done by traditional methods,” Leidy says. “The design charrette builds consensus and synergy, while a standard design approach can lead to misunderstanding and disagreement. We’ve proven that this strategy works again and again.”
With the charrette method of design, a typical week might include:
- Day One. Maintenance Design Group presents six or eight site layouts to its client’s work group to review. The sketches are put up on the wall, and everyone discusses what they like and don’t like about each. Once MDG has everyone’s comments, it takes the sketches back to the drawing board for the initial fine tuning.
- Day Two. The design team narrows the six to eight site layouts down to two or three. These new designs incorporate everyone’s comments and begin to show parking layouts, building details and preliminary landscaping features.
- Days Three to Five. Another review session and more refinements occur before Maintenance Design Group combines these last choices down to one final site layout. With the preliminary master plan in hand, the company turns its focus on the inside of the buildings. For the next two days, the company and the planning team review building interior options and discuss equipment needs in the same open forum until a conceptual design is agreed upon.
During the initial design phase, Leidy encourages fleet managers to hold a peer review session and invite other managers to a day-long informal review session asking them to critique the design. During this session, the peers can contribute any ideas that help validate the design for the managers.
“In one project, one peer administrator pointed out there was no place to push the snow,” says Leidy. “We already knew this was a problem because we were working with such a small site. As a result of the discussions from that meeting, we decided to install snow melt into the pavement, which solved our problem.”
Designing a maintenance facility is a complex process. “Asking the right questions and planning carefully in advance means fleet and managers will experience a smooth design and construction process that results in a safe, efficient and positive work environment that will last the life of the facility,” concludes Leidy.
3 solutions for parts storage
When it comes to planning for parts storage, two key considerations should be inventory availability and proximity of inventory, advises Jeff Sass, general marketing manager for Paccar Parts. Peterbilt and Kenworth dealers use these factors when designing their maintenance shops.
When working with dealer development teams, Paccar Parts has been able to identify three proven solutions for a more efficient maintenance shop, Sass says:
- Availability of parts to support the service department - The dealer’s parts department should have enough room to provide adequate warehouse or storage space. “Strong inventory improves the service department’s efficiency and makes it much easier for your shop to have the parts your customers need when they need them,” he points out.
- Quick access to high-usage parts - The shop and the parts storage or warehouse should be arranged in close proximity so shop technicians can easily access the parts they need, particularly high-usage parts.
“The back counter and front counter should be positioned fairly close to each other. That makes it easier for parts clerks - or parts runners - to respond to your customers and to your service technicians.”
- Effective use of information technology - Computers should be networked and located where service technicians can use them without leaving the service bays. “Technicians can then order parts electronically, which can reduce delays for your customers,” says Sass.
Space requirements
Obviously, the layout of any vehicle shop will be governed by the type of work that will be performed there, as well as by management’s expectations and requirements for the facility.
Among the many considerations:
- Administrative office space for fleet and maintenance personnel.
- Lunch and conference rooms.
- Locker and toilet facilities.
- Parts/tools supply and storage.
- Technician working space.
- Type and quantity of equipment required.
- Proper clearances and additional room for vehicle maneuvering.
- Provisions for drainage systems that prevent toxic waste from getting into storm drains.
- Water and energy conservation strategies.
- Heating, air conditioning, exhaust and ventilation systems.
- High and low pressure lubrication delivery systems.
- Type, location and quantity of vehicle lift systems.
- Specialty bays, including pressure cleaning and wash bay, body repair shop, paint and lettering bay, engine and accessories overhaul bay, tire service and repair bay and service station facilities.
- Overall electrical and power requirements.
- Equipment parking and open storage areas.
About the Author
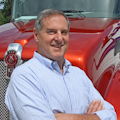