Need diesel techs? Try the three-step apprenticeship approach
Finding and recruiting the top-notch commercial vehicle technicians that shops need can be difficult to say the least, especially when what new techs say they can do and what you see are completely different.
“It's one thing to put [your skills] on a resume; it's another thing to see it in action," said Sasha Spencer, operations manager at KTS Enterprise, a mobile and in-shop diesel service provider based in the Phoenix area.
Spencer noted that the shop does have a solid training program to teach technicians the company's procedures, "but at the same time, it's really hard to find people who are already qualified and have experience.”
What happens is you get techs who are very skilled at preventive maintenance, but might initially struggle with higher-level repairs, Spencer noted.
To solve this problem, shops can establish apprenticeship programs, allowing them to train the techs they need from the start. First they need to know from where to source their technicians and the parameters in which they’ll operate, then they can reap the rewards of having homegrown quality techs instead of hoping resumes and reality match up.
Step one: Finding the right people
An easy place to look for potential apprentices is at local high schools and vocational schools.
“We have relationships with a couple of close high schools and technical schools that we work with,” said Jake Nunn, co-owner of North Jersey Diesel Repair & Performance(NJDRP), a diesel repair shop focusing on Classes 3-8 vehicles. “They approach us with kids that are in technical schools or on work release programs, and we sign off on the paperwork to absorb the liability of having them on site.”
These students, usually 16 to 18 years old, then serve as an extra pair of hands around the shop. Rush Enterprises similarly recruits their apprentices, usually hosting one or two interns while they split their time with a technical training institute, said Mitch Davisson, director of service. At least, after they’ve gone through the interviewing and hiring process that any other technician would.
But shops don’t have to recruit potential apprentices from vocational institutions. At KTS, Spencer said their mindset is to recruit “specifically for people who do not have a lot of experience, but have a lot of one, the desire, and two, the ability to learn and build on that desire.”
Step two: Establish the apprenticeship structure
How a shop’s apprenticeship program is structured is where businesses have the most leeway to tailor to what they need. The structure’s flexibility can also vary based on demand and a shop’s availability to work with their trainees, as long as the topics covered are straightforward.
“The program's clearly defined and established on set courses, but the timeline is not,” explained Victor Cummings, VP of Service Operations at Rush Enterprises. “If it [takes] three months, six months, or nine months for the employee or candidate to complete the program, that's fine.”
Rush does require each intern to complete a certain amount of hours in particular areas, even if they’re more flexible on when those hours are completed. For the company, students spend about 200 hours in the program overall, with 20 hours spent shadowing each department plus 100 dry hours filled with training and working on the floor. Then, each apprentice has a check sheet as they progress through the program’s stages that the service manager must sign off on to confirm the apprentice’s competency.
Read more: Apprenticeships: The sustainable way to solve tech shortage
“We're not going to just get you in the shop and throw you with somebody and say ‘Hey, learn what you can,’” Davisson confirmed.
At KTS, their training program emphasizes repetition alongside hours worked. Their checklist has apprentices watching another technician do a task a certain amount of times, with the number of repetitions defined by the particular task. Then they’ll do the work under supervision a certain number of times, and once they can do so without errors, they’ll progress to handling the work on their own, with another senior technician to check their work, too. At the diesel repair operation, they usually start their apprentices on PMs, then chassis lubrication, lighting checks and repairs, and then on to air leaks and more advanced work.
But not all programs need to be quite so structured, especially if your apprentices are on the younger side. NJDRP apprentices spend roughly four hours at the shop, starting with two hours of basic housekeeping that ranges from garbage duties, sweeping, managing the oil disposal area, and filter removals.
“They are losing one to two hours a day between garbage duties, disposal, cleaning up,” Nunn said. “But for the rest of it, they're basically free for all.”
Now, the apprentices might deal with an oil change with another technician, handle greasing jobs, or, if they’re confident enough, they might work on a brake job on a pickup.
One tactic that’s likely to pay off in the long run is to make sure your apprentices are learning broadly, instead of only focusing on a specific task in the shop. Including duties even beyond the shop floor can also pay off in the long run.
At Rush, they make sure their interns spend time with a service advisor writing repair orders, then meet with the foreman to see how the truck arrives and is scheduled to a technician. Not only will they spend time doing hands-on training with that tech, but they’ll then head to the back office to learn about service managers’ jobs, and may even spend time with a warranty administrator or at the parts counter to understand parts estimates, billing, and parts pooling.
“The [program] encompasses the entirety of the service department and how that repair order is transitioned through the shop from beginning to end,” Rush’s Davisson added. “And they also get a little bit of time with those employees, so they build a personal relationship with them.”
Step three: Watch your shop staff grow
For NJDRP, KTS Enterprise, and Rush Enterprises, their apprentice programs have paid off in several ways. For NJDRP, having apprentices has allowed them to capitalize on their most experienced employees’ knowledge, and may impact their profits, too.
“We're gonna try to leverage that to the point of having maybe three or four lead technicians overseeing four to five apprentices,” Nunn explained. “And now you're quadrupling your amount of billable hours due to that because they need to learn.”
Meanwhile, KTS Enterprise’s work has allowed them to have a better understanding of their future techs’ strengths and weaknesses and hone their training to meet those needs.
“And that has also been great for retention as well, because I've had some of [our apprentices] say that they were very grateful for the opportunity to learn something, and they're still with us,” Spencer stated. “Some of them have even taken a pay cut to come and apprentice with us.”
Finally, Rush has been able to leverage their apprentice program to create more techs but also create back-ups for other jobs in the shop due to their cross-training, particularly for the service advisor position.
“If we're short-handed administratively, we can have an emergency backfill, if you will,” Cummings explained. And if the technician finds themselves gravitating towards the office side of the business, all the better, so that “the technician positions have been a good pipeline for staffing the service office.”
About the Author
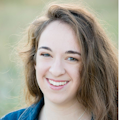
Alex Keenan
Alex Keenan is an Associate Editor for Fleet Maintenance magazine. She has written on a variety of topics for the past several years and recently joined the transportation industry, reviewing content covering technician challenges and breaking industry news. She holds a bachelor's degree in English from Colorado State University in Fort Collins, Colorado.