Slightly loose or corroded wires, worn tires and brakes, and other small problems on a truck can become worse after hitting rough patches on the road or when the weather changes. And those can transform into noticeable issues a safety inspector will definitely catch during a walkaround, with the fleet’s CSA score taking a hit and the truck put out of service until the violation is corrected.
And if your driver is involved in a collision, undermaintained brakes and tires will have a far worse impact than an out-of-service violation.
“It is, of course, worrisome to carriers when they receive these violations, but the violations are actually the smallest part of the problem for them,” Jeremy Disbrow, roadside inspection specialist for the Commercial Vehicle Safety Alliance (CVSA), told Fleet Maintenance. “The bigger problem is the potential liability for them if there is a collision. Even if the CMV is not the ‘at fault’ vehicle, they will likely be sued if there are brake defects discovered during a post-collision investigation, and those lawsuits can be devastating to any motor carrier.”
But these areas are problems for many fleets. CVSA placed about one in five vehicles out of service during its annual International Roadcheck in May. The top issues in the U.S. were related to brakes (42.9%), tires (22.1%), and lights (12%).
Yet all of these are issues that should be caught during pre- or post-trip inspections and then logged on driver vehicle inspection reports (DVIRs). This is particularly important because DVIRs are required by Federal Motor Carrier Safety Administration regulations for commercial vehicles and buses over 10,000 lbs. GVWR, and those that carry nine or more passengers or transport hazardous materials.
When done correctly, DVIRs provide an instant snapshot of a truck’s safety readiness. Because safety is so important, many fleets are opting to implement electronic DVIRs (eDVIRs) so the data is digitized and instantly accessible to those other than the driver or the last person to inspect the vehicle. Customizing these DVIRs specifically for your fleet could not only lower CSA scores but also streamline repair workflows.
Using Whip Around’s fully customizable eDVIRs platform has helped Maletis Beverage identify issues before trucks and trailers leave the yard, said Mick Peckham, Maletis warehouse specialist. The Pacific Northwest beverage distributor fields about 80 straight trucks and trailers.
“All reported defects go straight to our mechanics, and most can be repaired within 24 hours, so those daily inspections help us keep repair costs and downtime to a minimum,” Peckham said. “When small issues can be quickly identified and resolved before becoming major and/or costly fixes, our fleet is up and operating, and we can keep lost profit to a minimum.”
Customized electronic records also allow operations to adapt inspections by state and access those records more easily.
“Our warehouse managers can easily select a team and pull a compliance report for any time period to ensure proper inspections are being completed during each shift,” Peckham explained.
The Doughnut Peddler, a commercial bakery based in Chandler, Arizona, uses Fleetio’s customizable eDVIRs to monitor its 292 trucks, which deliver product nightly to more than 4,000 convenience stores in five states. Tim Mele, distribution market manager for Doughnut Peddler’s Texas and Tennessee region, reported that Fleetio eDVIRs are in place to document pre-trip inspections by every driver.
“The eDVIRs are reviewed daily by location supervisors and the distribution market manager,” Mele said. “This gives us the ability to identify any safety concerns or potential repairs early to save on excessive costs by something going unseen.”
Aside from the typical pre- and post-trip inspections, the bakery’s trucks must also adhere to a rigid cleaning schedule to retain Safe Quality Food Program certification, and Mele said they created a specific inspection for that as well.
Customizing for specific fleet needs
Ron Cordova, director of safety and compliance at Zonar, noted that the ability to customize inspections is particularly important for vocational fleets. For example, construction or utility operations have specialized equipment mounted on vehicles that need to be inspected in addition to regular items.
“The Inspection Builder feature of our EVIR solution allows fleets to modify or create inspections tailored to their specific needs while maintaining compliance,” Cordova explained further. “This flexibility enables them to integrate unique protocols, such as tag placements and specific component inspections, and align inspections with company-specific language and policies.”
Zonar says its customized solution overall can reduce inspection time by 50%, time that can now be used putting the truck to work.
In addition, the Inspection Builder allows fleets to build more robust inspections around areas such as tires and brakes.
“With EVIR technology from Zonar, we’re better able to track missing and failed inspections, and defect and maintenance reporting,” said Timothy Parson, lean engineer, department of safety and quality assurance at the Metropolitan Atlanta Rapid Transit Authority (MARTA), which operates 530 buses in the greater Atlanta area. “These data-driven insights have helped us achieve quantifiable improvements in operational efficiency and cost savings, which ultimately helps us ensure safer, more reliable buses.”
Read more: It’s time to reinforce inspection basics
Paul Cardosi, VP of the mobility division and general manager at Trimble Transportation, reiterated how important it is for fleets to have flexibility based on their operations and industries.
“Our digital DVIR solution for fleets, Trimble Inspections, enables fleet and safety managers to create configurable checklists based on load and truck type as well as specific business needs,” he said.
Trimble Inspections also allows fleets to add or edit driver focus areas and provides the ability to reorder checklists to follow the natural flow of an inspection. “This allows drivers to inspect assets using easy-to-follow workflows configured for their specific journey, eliminating unnecessary steps often contained in standardized inspection systems,” Cardosi added.
Dan Simpson, Fleetio’s senior product marketing manager, suggests flexibility as a key feature to look for in an eDVIR. Customized eDVIRs allow a mixed fleet to “create and assign unique inspection items in our eDVIR tailored for each asset type,” he said.
“Once an issue is reported, you also want to be able to take action,” Simpson continued. “eDVIR systems should allow you to set up custom alerts and workflows to resolve problems quickly. If a driver logs a critical defect, you want a system that can allow you to assign priority and send it directly to your maintenance team.”
Mele said The Doughnut Peddler has created many eDVIRs in addition to the standard pre-trip inspections for drivers. “For example, we have daily supervisor inspections for the fleet during which notes on each truck can be made, and a vehicle’s status can be changed if needed,” he explained. “Using this when a DMM is in the field, we can evaluate our supervisors’ use of Fleetio as well as the status of the fleet.”
Emily Williams, head of Transportation Business Development, Geotab, pointed out that the company’s eDVIR solution goes beyond simply checking boxes on a list. “It automates the inspection and reporting process, ensuring easy and efficient compliance through report logging and certification,” she said. “In addition, by leveraging features like predictive maintenance, fleets can identify and address issues before they lead to costly repairs or violations.”
Integrated value
Fleets can also customize these inspection tools to integrate with their operation’s unique workflows.
“Whether it’s requiring drivers to capture live photos or adding inspection items for specialized equipment, the flexibility to build an eDVIR process for a fleet’s operational needs minimizes downtime,” Debbie Bain, Whip Around chief marketing officer, noted.
“By integrating eDVIR data into back-end systems, maintenance teams can proactively assemble work orders,” Geotab’s Williams added. “An integrated system streamlines maintenance, improving fleet efficiency and reducing downtime.”
With integrated inspections through DVIRs, issues reported by drivers can trigger real-time alerts for fleet managers, Fleetio’s Simpson said. “eDVIRs also support preventive maintenance by automating service schedules based on vehicle use and reported issues,” he said.
“When integrated with fleet maintenance software, eDVIRs can automate repair workflows,” Trimble’s Cardosi stated. “Effective eDVIR use also creates a record of repairs and inspections, which is crucial for keeping a closer eye on vehicle health and identifying recurring issues throughout the fleet.”
This allows fleets to complete repairs as they come up during inspections, reducing the potential for roadside issues and bolstering a fleet’s reputation and employee retention.
“Shippers want to work with carriers who get their goods from Point A to Point B reliably,” Cardosi explained. “Roadside breakdowns due to unaddressed maintenance issues can delay shipments, and if those are a frequent occurrence, carriers run the risk of losing a customer.”
Paper-based inspection systems also make it difficult for managers and maintenance teams to determine if any part of the inspection had been rushed or overlooked, noted Zonar’s Cordova.
“With digitally verified EVIR solutions, fleets streamline the process, reduce errors, and get faster, more reliable results,” he said, because EVIR can increase inspection accuracy and standardization, helping drivers to identify maintenance issues early and keep vehicles on the road.
With an effective eDVIR system in place, drivers can report issues in real time, related Dan Simpson at Fleetio. “This way, maintenance teams can fix problems before they become costly issues that can result in fines or out-of-service violations,” he said.
eDVIRs can also mitigate disruptions to fleet operations and increased costs, related Williams at Geotab. “Effective inspections also help ensure that safety-critical issues are addressed in a timely manner, minimizing the risk of violations and fines, which can drive up insurance premiums and increase scrutiny from regulators,” she said. Not to mention improve relationships with customers who prioritize safety and reduce driver frustration with consistent equipment failures, she added.
Whip Around’s Bain summed up the value of effective inspection practices: “With eDVIRs, fleets can identify and resolve potential issues before they become big problems that lead to hefty fines, significant downtime, or even crippling litigation,” she stated. “Proactively managing vehicle maintenance through eDVIRs prevents violations, avoids towing costs, repair delays and reputational damage, and also helps ensure businesses stay operational and profitable.”
About the Author
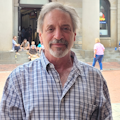
Seth Skydel
Seth Skydel, a veteran industry editor, has more than 36 years of experience in fleet management, trucking, and transportation and logistics publications. Today, in editorial and marketing roles, he writes about fleet, service, and transportation management, vehicle and information technology, and industry trends and issues.