Running a fleet maintenance operation has never been inexpensive. Service shops need lots of parts, supplies, software, tools, and equipment to keep today’s commercial vehicles up and running. And inflation over the past few years has driven many of those costs up.
A shop needs some really good technicians, too. Given the scarcity of qualified techs and the 24,000-plus job openings projected each year, the natural law of supply and demand has pushed wages up. In fact, according to the U.S. Bureau of Labor Statistics, the average wage for a diesel service technician is around $28/hour. That’s up about $4/hour since 2020.
With all of this overhead creep impacting the average shop’s finances, some may find it difficult to keep up with the need to upgrade service equipment. But planning and budgeting for the right equipment has never been more important. After speaking with several fleet professionals, we discovered that just like with vehicles and parts, there are some areas where spending more up front on premium brands pays off in the long run. But where exactly?
Every shop is different, so this will vary, but the core motives should be to support technicians while improving uptime and safety.
Team-oriented approach
The first step is planning how to find which equipment investment will have the most impact. Analyzing what to plan for and spend on should not be done in a silo. Talk to the people who run each of your locations, and consider their feedback.
“Feedback can pinpoint specific areas where equipment upgrades or new tools are necessary,” said Max Farrell, CEO and co-founder of WorkHound, an employee feedback platform. “By understanding workplace challenges and inefficiencies from the workforce’s perspective, managers can prioritize investments that will have the most substantial impact on productivity, safety, and employee satisfaction.”
Read more: Product Showcase 2024: Shop Equipment and Supplies
Joey Young, fleet maintenance operations manager for Publix Super Markets, oversees roughly 400 technicians and support staff working in 10 maintenance shops across four states. It’s too much for him to handle all of the retooling on his own. He said it requires a team-oriented approach, noting each Publix shop is responsible for operations and the required tools, supplies, and equipment needed to complete them.
“Each individual brings forth the things they think they need,” Young said. “We review all of that as a team before entering it into a three-year planning document. I review that plan with my leaders and peer group to prioritize different items by year.”
This approach allows Young and his colleagues to have a highly accurate view of what the next three years will look like.
“Overall, I get a lot of what I request because I have great support from leadership,” Young said. “A big reason why is that we take the time to do the planning; we don’t just throw everything against the wall to see what sticks. We know what our priority items are, and we know how to explain their importance to leadership.”
Of course, to make these informed requests, it’s critical to have a way to consistently collect employee feedback on equipment without disrupting their work. WorkHound’s answer to this is an anonymous platform with two-way chat capabilities and an analytic dashboard to organize feedback. This creates what Farrell called “a continuous feedback loop” for equipment needs, making it easier to understand and plan for future purchases for both local shop management and executive decision makers.
“Detailed feedback provides concrete examples and data that can be used to justify capital investments to stakeholders,” Farrell emphasized. “For instance, feedback highlighting frequent equipment breakdowns, safety concerns, or dips in productivity can support the need for new purchases or upgrades in a way that considers business needs.”
After all, these equipment purchases are not just expenses but investments in future shop productivity. Spending money on a useful tool, technology, or piece of service equipment can actually help a fleet save money in the long run.
The challenge is figuring out the items that will provide the biggest payback in terms of how often they’ll be used and if they’ll help make technicians safer, happier, and more efficient.
Here are the two major areas our sources said can positively impact technician job satisfaction and shop productivity:
Tire service and alignments
“Our shop does pretty much everything but overhauls,” said Miguel Miranda, fleet maintenance manager at HD Repair in Plainfield, Illinois, the maintenance division of OTR provider MNS1 Express. “We have a very robust PM program. There is certain service equipment we’ve found that aren’t just beneficial to our operation, but are integral.”
Procedures like alignments and wheel balancing have become part of the routine preventive maintenance schedule at HD Repair, especially when steer tires are replaced. HD Repair has been using Hunter alignment equipment for the past year or so. Miranda said it’s been relatively easy for technicians to learn to use.
Additionally, because of the sheer volume of tires that are handled on a regular basis, Miranda has sought out equipment that gives his technicians a literal helping hand when servicing tires.
“We have close to 400 trailers,” Miranda said. “Our shop typically mounts and dismounts 30 to 40 tires a day, and that’s just for trailers. We’ve thought about just outsourcing tire service but decided to keep it in-house to maintain quality. But in order to do it in-house, we needed to bring in a tire-mounting machine. If I asked a technician to manually mount and dismount that many tires in a day, he probably wouldn’t be working for me much longer.”
HD Repair uses Hunter tire-changing equipment. Miranda likes how the machine is laid out and how the levers are positioned with efficiency in mind. He also likes that the equipment can be adjusted to accommodate different technician heights. As Miranda noted, it’s all about efficiency, and efficiency isn’t just a matter of one technician doing one tire faster.
“Efficiency comes down to consistency, tire after tire after tire,” Miranda said.
Publix maintenance facilities also have equipment for servicing tires. “We almost look at this type of equipment as another safety item,” Young said. “Tire mounting and dismounting can be a pain point with respect to ergonomics and technician safety.”
Publix maintenance facilities have also standardized with the Hunter brand.
“They are robustly built, we don’t have a lot of problems, and they last,” Young said. “They are very good ergonomically and easy for our technicians to work with. There are other good manufacturers out there, and we have tried a couple of others. But Hunter has met our needs so that’s what we stick with.”
Heavy-duty jacks and lifts
Shop size may also influence the types of service equipment that are brought in. Sometimes there isn’t much room to house a lot of bulky equipment. Also, the services provided are often rather narrow when dealing with a smaller staff.
“Our shops are generally smaller, with three or four technicians on average,” said Kirk Altrichter, EVP of fleet services for Kenan Advantage Group (KAG) in North Canton, Ohio, which operates a large Class 8 fleet of primarily tanker trucks. “Our shops are more focused on what I call the bread-and-butter items like tires, lights, brakes, and routine PMs.”
Given that core competency, Altrichter’s maintenance team has identified a key item that not only makes technicians more efficient and productive but also safer.
“An air/hydraulic jack is a huge time-saver,” Altrichter said, adding that it’s one of those technicians have continually requested over the years. “If you get enough people saying the same thing, they’re probably right. That’s why we want high-quality equipment, not something cheap that won’t even last a year. We’re more focused on total cost of ownership (TCO) than just the upfront cost.”
Along with the upfront purchase price, TCO factors in the recurring costs of maintenance and repairs over the life of the equipment. Loss of technician productivity when a jack goes down must also be considered.
Altrichter’s shops have gone with Gray Mfg. jacks and jack stands because of their good reputation. After proving that equipment out in some of KAG’s shops, Altrichter said they’ve made it standard. “We’ve tried some knock-off brands before,” he said. “I kept seeing repair bill after repair bill. It was constant replacement, and that’s exactly what we want to avoid.”
For Blaine Brothers, which provides parts, repair, and towing services in Minnesota and Wisconsin, mobile column lifts have proven to be a worthwhile investment given the wide range of maintenance and repair services they routinely provide.
“Mobile column lifts have been a big help in gaining efficiencies,” said Tim Grabow, president of Blaine Brothers. Benefits of this type of lift include its mobility, which allows technicians to set it up and move it out of the way as needed. Additionally, the columns can be configured in different ways to accommodate different types of vehicles.
Blaine Brothers started with some used lifts when they moved into a new service facility.
“We saw immediate improvements in efficiency, so now we incorporate them everywhere we can,” Grabow said. One caveat is that a shop has to be big enough, with a high enough ceiling to accommodate a truck lift. Not all Blaine Brothers shops meet that prerequisite. But for those that do, mobile column lifts have become a staple item.
“The newest lifts we have from Rotary are battery-powered,” added Jason Kendrick, director of service operations for Blaine Brothers. “That has helped gain some additional efficiency during setup because nothing has to be plugged into the wall, and everything links together wirelessly without any cords. Then, once a vehicle is in the air, everything is easier on the technician. This type of lift is a little bit pricier than some, but the added convenience makes it worth it.”
In part two, we'll cover other support equipment that you may want to consder upgrading.
About the Author
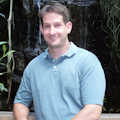