Safety Is Always Important When Operating Vehicle Lifting Systems
All vehicle maintenance shops strive for maximum efficiency in all that they do and lifting systems used to raise vehicles for repair and diagnosis can represent one of the most productive tools in a shop, maintains Steve Perlstein, president of Mohawk Lifts, a leader in lift technology (www.mohawklifts.com). Or, lifts can be one of the most dangerous pieces of equipment technicians use if they are not operated and maintained properly.
Not only does it make the technician’s job easier, but vehicle lifts improve performance, revenue and safety, provided the right type of equipment is chosen to best suit the application and is versatile and durable so the shop can benefit from its addition, adds Radu Pop, market research analyst and heavy duty equipment specialist with MAHA USA, a producer of lifting systems for both the automotive and heavy duty markets (www.maha-usa.com).
When selecting a lifting system, there are a few major factors that need to be analyzed before making the decision.
One is shop environment, including floor surface, ceiling height, power availability, access to the designated work area, space availability and position in the shop, Pop says.
Prior to selecting a lifting system - whether it is comprised of mobile columns, two-post, four-post, in-ground scissor or piston-style lifts - measure the ceiling height in the shop, says Dr. Jean DellAmore, president of Stertil-Koni USA. Stertil-Koni is the global market leader in heavy duty truck and bus lifts (www.stertil-koni.com).
Also note the height of the tallest vehicle that will be serviced on the lift, he adds. In that way you can determine if there is ample room to raise the vehicle to a serviceable height that will permit a technician to comfortably work underneath the vehicle.
Another factor that needs to be considered, says Pop, is the lifting capacity, method of engagement and service jobs to be performed.
Double-check the weight of the heaviest vehicle that will be lifted and “make absolutely certain” that the vehicle lift you select is certified to meet, or exceed, that threshold, advises DellAmore.
Type of equipment - fixed, mobile, plugged in or battery powered - also needs to be decided upon, Pop says.
In addition, DellAmore recommends selecting a lifting system that prevents unauthorized access to lift operation. This could take the form of a locked control box or a secure key or “wand” necessary to activate the lift system prior to use.
Then there is the matter of budget and getting “the most bang for your buck,” says Pop. The most important aspect is quality, but maintenance requirements and operational costs also need to be taken into consideration.
There are a lot of options out there and competition is fierce, especially now when price has become a major factor, he continues. This can work to your advantage. You might get a high-quality lift at a reasonable price, whereas in the past you would have had to spend a lot of money.
But price can also work against you, he warns, because buying a “cheap” lift may end-up costing more down the road in maintenance and operating costs, downtime and lost revenue, plus safety may be compromised.
BUY CERTIFIED LIFTS
One way to ensure that you are buying a quality lift is to make sure that it is certified, says Mohawk’s Perlstein, and there is only one nationally recognized safety standard for vehicle lifts: ANSI/ALI ALCTV.
These acronyms stand for the American National Standards Institute, Automotive Lift Institute and Automotive Lift Construction, Testing and Validation, respectively.
This standard is administered by the ALI, a trade association of vehicle lift manufacturers which works with a nationally recognized independent testing laboratory to verify that lift manufacturers meet and comply with accepted industry safety and performance standards, he says.
The testing includes verification of the structural integrity of a lift’s systems and components, proper function of its controls and appropriate lowering speeds and overload protection.
To verify a lift’s status, look for the gold “ALI Certified/Validated by ETL” label on it, advises Perlstein. This label indicates that the lift has been tested and certified to meet the current ANSI/ALI ALCTV standards.
It is legal in North America to sell lifts that do not meet the ANSI safety and performance standards, points out John Rylee, director of marketing for Rotary Lift, the leading brand of vehicle lifts and equipment designed to increase technician productivity (www.rotarylift.com). Installing non-certified lifts, however, is another matter.
In the U.S., building codes in all 50 states and Washington, DC, require that any lifts installed be certified, he explains. These states and many Canadian provinces have adopted the International Building Code (IBC) which specifically requires that all lifts be certified to the ANSI/ALI standards. If a non-certified lift is being used in one of these areas, building inspectors are authorized to tag it out of service.
BE SELECTIVE WITH LIFT OPTIONS
A commonly overlooked mistake is using an uncertified option or accessory on a certified lift, observes Perlstein of Mohawk. Doing so will void the lift’s certification and could put safety and lift performance at risk.
ALI/ETL, ANSI and IBC standards require that all accessories, such as rolling jacks, truck adaptors, lighting for runway lifts and special lifting pads, be certified, he says.
Although certification is good for the life of the lift, older models may not meet the most current standards, which typically change every five to seven years, he adds. Some lifts and options that were certified in 2000 wouldn’t pass the 2011 ANSI/ALI ALCTV standard.
TRAINING IS KEY
Training those who will be operating vehicle lifting systems is essential, MAHA USA’s Pop stresses, because no matter how advanced the lift is, its operation is defined by a user.
ANSI requires that technicians be trained annually in proper lift use, add Mohawk’s Perlstein.
Each lift comes with an operator’s manual and additional lifting safety manuals that are required with the delivery of a certified lift, they both note. Yet, many shops tend to disregard those manuals and start using the equipment without being aware of proper safety procedures, says Pop.
Accidents have happened and more than 90 percent are caused by operator error, he points out. Proper training will ensure safe and efficient operation and prepare the user for an emergency situation. What’s more, by using the lift right, service life will be extended.
PROPERLY OPERATE THE LIFT
Most lifts have an overload protection, says Pop of MAHA USA. However, common sense should prevail and the user should make sure the lift is not overloaded and that the weight is distributed evenly or centered properly when using mobile wheel-engaging lifts, also known as mobile column lifts.Mobile wheel-engaging lifts utilize individual lifting columns that are used in sets of two, four, six or more units, he explains. Each column is mobile and contains an electric power unit interconnected with the other columns. A master control unit synchronizes all columns so that they operate in unison.
With mobile column lifts, before you begin, always lift on a firm foundation on level ground, Stertil-Koni’s DellAmore recommends. When lifting outdoors, be aware of wind loads. Also, make certain that all personnel are clear of the vehicle and that the wheels on the vehicle being raised are properly engaged with the forks on the mobile column lifts.
For in-ground piston lifts and axle-engaging scissor-style lifts, operators should check that the contact points are properly positioned, he says.
While many mobile wheel-engaging lift manufacturers offer capacities of more than 18,000 pounds per column, tires are rated at a maximum of 14,500 pounds, Pop points out. Always check tire pressure before lifting and make sure rated tire capacity is not exceeded during the lifting operation. The user also needs to check the surroundings and ensure that there’s enough ceiling clearance to perform the lifting operation.
LOCKING MECHANISMS
Typically, heavy duty vehicle lifts are equipped with mechanical locks, especially hydraulic units, and they need to be used, stresses Mohawk’s Perlstein.
There is the saying: “Never use a jack without a jack-stand,” he says. The same principal is true for vehicle lifts. Always raise the vehicle and then lower it onto the lift’s mechanical locks as required by ANSI. Refer to ALI materials or the lift manufacturer’s operating instructions for detailed information.
Keep in mind that hydraulics are used for lifting, not for support, says Pop.
Technicians ought to visually verify that the mechanical locks are fully engaged, Perlstein says. Another way to confirm the locks are being used is to include a weight gauge - a pressure gauge calibrated to the lift’s lifting capacity - on the lift.
Most mechanical ball-screw lifts will not require a mechanical lock as they are designed to support, notes Pop. However, a safety wedge is present on these units as a redundant safety feature that will engage only in case of emergency.
REGULAR CARE
The best way to maximize the return on investment after buying any lift system is to properly maintain and inspect the equipment, concur Perlstein, Pop and DellAmore.
Most operator’s manuals have a periodical maintenance procedure, they point out. The lift manufacturer or their field representatives can be contacted for information and correct maintenance procedures, they say.
Keep the equipment clean and lubricated and it will have a long service life, concludes Pop. Also check for signs of wear and mechanical failure associated with aging. Lifts get old too, so any wear items like cables and rollers should be inspected periodically and replaced when necessary.
CERTIFIED LIFT INPSECTORS
The ALI recently developed its Lift Inspector Certification Program. While annual vehicle lift inspections conducted by a “qualified automotive lift inspector” are required by the ANSI National Standard covering vehicle lift operation, inspection and maintenance, until the program was launched there had been no national vehicle lift inspection licensing or certification programs.
Proper vehicle lift certification, installation and inspection have come under increased scrutiny in recent years by OSHA and other local, state, provincial and federal health and safety officers, explains R.W. “Bob” O’Gorman, ALI president. This has resulted in an increase in shops looking for qualified automotive lift inspectors.
Without a national certification program in place, vehicle lift inspection companies haven’t been able to offer independent validation that their inspectors are qualified, he says. The Certification Program will provide third-party assurance that a Certified Lift Inspector has been tested and proven competent to thoroughly inspect an installed vehicle lift and report on its suitability for continued use and/or the need for maintenance or repair.
About the Author
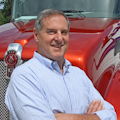