Fuel contaminants, and sub-par fuel in general, can cause problems for fleets. The good news is that a few simple steps can be taken to help avoid many issues.
“Impurities in a fuel system will reduce engine power and fuel efficiency and cause uneven engine performance,” said Phil Cary, southeast regional fleet service manager for Mack Trucks, a manufacturer of heavy-duty trucks, engines, and transmissions. “Chemical or dirt debris can also cause significant damage to all fuel-carrying components, from the fuel tank to the injectors.”
“Diesel fuel impurities can also lead to fuel system deposit formation, plugged fuel filters, and the growth of microbes in the fuel,” said Eric Trimble, product manager at Lubrication Specialties Inc. (LSI), maker of Hot Shot’s Secret fuel and oil additives. “Impurities can also lower a fuel’s lubricity properties.”
“Water in the system can cause frozen or gelled fuel in filters and lines, which results in reduced power or even the engine shutting down,” said Clay Parks, vice president of development at Rislone, a maker of additives and treatments for fuel, engine oil, and transmission fluid.
All of these issues can financially impact a fleet in various ways. Mechanical failures require expensive part replacements, not to mention the cost of extensive downtime. “Consistent water contamination and microbial growth in bulk tanks can lead to additional treatment costs, like a biocide or water dispersant,” Trimble added.
In addition to water and microorganisms, Cary pointed out that diesel fuel can contain other contaminants including wax in cold weather, hard particles, debris, and other sediments. Diesel exhaust fluid (DEF), accidentally added to the fuel tank instead of the DEF tank, is another source of contamination that happens all too often.
Warning signs to watch for
There are steps a fleet can take to help prevent fuel issues from turning into fuel system issues.
“I always stress the importance of solid driver-technician feedback to help identify intermittent issues,” said Nick Rivera, a commercial vehicle lubricants application engineer with ExxonMobil Fuels and Lubricants. “With any potential fuel-related issue, I would first ask the driver if he or she has detected a significant loss of performance. A driver would likely notice some kind of derated engine output such as stumbling, erratic idle, poor acceleration, excess smoking, and even more frequent aftertreatment regen sets.”
Aside from gathering driver feedback, technicians have other steps they can take to identify fuel-related issues.
“Performing a simple visual check of the fuel separator is important,” Rivera said. “Is there excess sludging? Is water showing up periodically? Another thing to look at is if there are any signs of film inside the tank, whether that’s water or some kind of microorganism that’s growing.”
Fuel injectors represent another area technicians should pay close attention to.
“High-pressure common rail fuel injectors are susceptible to abrasive wear particles typically found in the 4- to 15-micron range,” said Jay Stephenson, North American training leader for Cummins Filtration, a global leader in air, fuel, hydraulic, and lube filtration. “Sacrificing filter performance to save a few dollars can come back to haunt a fleet when the fuel system starts experiencing problems.”
Stephenson pointed to an example where failing injectors can lead to fuel washing the lubricating oil off the cylinder walls, which enables metal-on-metal contact between the power cylinder components during combustion.
“Injectors that are not maintaining correct injection pressures will spray as a fine mist, struggling to atomize fuel properly,” Stephenson said. “The first signs of injector wear are hard engine starts and rough idling. But as this continues, increased fuel consumption, loss of horsepower, and increased emissions are common signs that injector wear is in advanced stages and may be nearing failure.”
Malfunctioning injectors can also lead to an abundance of soot due to over-fueling. “That can prematurely clog the diesel particulate filter (DPF) and cause the aftertreatment system to throw codes,” Stephenson said. “In terms of the filter directly, if premature plugging or short filter life are experienced, it’s often an indication that the cleanliness of the diesel fuel in the tank is poor.”
Tips on proper fuel filtration
As Cummins Filtration’s Stephenson pointed out, the only proven method for combating dirty fuel is through effective filtration techniques using a combination of multi-stage filtration fuel filters when possible: stage 2 (on-engine), stage 1 (fuel-water separators which are typically chassis-mounted), and stage 0 (bulk fuel storage tanks) fuel filters.
For fuel fill-ups on the road, stage 0 filtration is not realistic. But for fleets operating their own fueling sites, Stephenson said stage 0 filtration and routine bulk tank storage cleaning are best practices for ensuring cleaner fuel.
For any fleet, Stephenson said it is always imperative to use a stage 1 fuel filter/water separator, such as a DAVCO Diesel Pro or Fuel Pro unit, in combination with a stage 2 on-engine fuel filter, to ensure that the stage 2 fuel filter can achieve its rated service interval. “Without a stage 1 fuel filter/water separator, the stage 2 filter will take the brunt of all fuel contamination and will be quickly overwhelmed,” Stephenson explained.
Some Cummins Fleetguard stage 1 fuel/water separator filters are constructed with a three-stage water-removal architecture to combat the severe challenges of water in diesel fuel. Stephenson said this filter design also helps fleets meet the requirements for advanced water removal on 2017 and newer U.S. EPA model engines.
Even when utilizing premium-quality fuel filters, technicians must still adhere to proper filter maintenance and changeout intervals.
“Engines that have a fuel/water separator should be drained on a periodic basis,” ExxonMobil’s Rivera said. “The frequency depends on the amount of fuel the truck consumes, as well as the amount of fuel a fleet with on-site storage purchases. As a general rule, the fuel/water separator should be drained at the same time the regular fuel filter is changed.”
Fuel filter replacement intervals will vary based on several factors. “How often a fuel filter must be changed depends on geography, fuel type, and other factors,” Rivera said. “I see recommended intervals ranging from 12,000 to 25,000 miles depending on the OE. Know what the recommended interval is, and always use an OE or OE-quality filter.”
Before a technician even touches a fuel filter, River said it’s critical to clean the filter housing and surrounding area to remove any dirt or other contaminant buildup. “It’s really important to have good housekeeping procedures to prevent contamination of the new filter you’re installing,” Rivera added.
A little additive can go a long way
Clean, high-quality fuel is key to maximizing vehicle performance. Trimble, of Hot Shot’s Secret, said fleets should search for a fuel that is consistently strong in the following categories:
- Cetane number
- Lubricity
- Corrosion protection
- Injector deposit control
- Low-temperature operability (October to March)
- Filter-blocking tendency
- Thermal stability
“Running a fuel without the proper cetane number can result in lower fuel economy, rougher operation, and less power,” Trimble said. “Fuel without proper lubrication can lead to catastrophic failures such as fuel pumps and injectors. Diesel fuel that cannot adequately control injector deposits will lead to deposits forming both internally and externally on fuel injectors. These can lead to fuel delivery issues, rough operation, and wear.”
Fuel additives can help combat these potential issues.
“General-purpose diesel fuel additives are designed for use all year, while others are specifically formulated for certain seasons or particular issues,” Rislone’s Parks explained. “For example, cold-weather driving requires the use of anti-gel additives to keep fuel from gelling and clogging the fuel tank and filters. This can be especially important in the winter when southern trucks travel north. There are also special water removers that work in combination with anti-gel additives to keep fuel lines from freezing up.”
Cetane additives also exist to help boost engine power. Upper cylinder lubricants help reduce friction. “This is especially helpful in older diesel engines that were not specifically designed for ultra-low sulfur diesel (ULSD) fuel,” Parks pointed out. “A lubricant also keeps fuel pumps running smoothly.”
Sometimes a fleet has more than one fuel-related issue to contend with. In those instances, Trimble said a fully-formulated additive that isn’t full of fillers can be an efficient and cost-effective solution. Examples include Hot Shot’s Secret Everyday Diesel Treatment and Rislone Hy-per Diesel Complete Fuel System Treatment.
ExxonMobil’s Rivera reminded that it’s always essential to refer to the OE manual for advice on what should and shouldn’t be used.
“Some manufacturers don’t allow for the use of certain aftermarket fuel additives in their engines,” Rivera pointed out. “Some OEs feel that diesel fuel that meets ASTM D975 is sufficient for most conditions.
“At the end of the day, an individual fleet has to manage this decision for itself,” Rivera continued. “If you have on-site bulk tanks and are having issues with water intrusion or microorganisms affecting your fuel, your next recourse is going to be some kind of additive treatment. In a perfect world, 2D gets refined and is delivered to the end-user in a refined condition. But time is the enemy. Add to that some severe fluctuations in temperature, and some kind of degradation is likely to occur. Plus, you never know when other types of contaminants might enter the supply chain.”
That is precisely why fleet technicians should always be on the lookout for symptoms of fuel-related issues.
About the Author
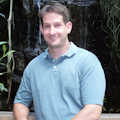