How processes and guidelines improve repair quality
This is Part Two of a two-part story.
While perfect repair accuracy every time a vehicle comes into the shop is a high goal, there are best practices shops can put in place to ensure they come close to perfection. In Part One of this story, we discussed how shops can measure and analyze where they're missing the mark and how often. Next, maintenance managers need to apply this data to help their technicians stay on track during repairs, whether that means ensuring complete and thorough communication between drivers and technicians or establishing checklists to keep technicians focused during the job.
We spoke to experts from shops, fleets, and fleet associations to help fleets develop the processes they need to keep their repairs accurate and comebacks to a minimum.
Starting off right
The first step to avoiding a customer comeback is to make sure technicians are aware of all the repairs a truck needs. Just because all the concerns listed on a work order were handled doesn’t mean all the truck’s issues are fixed. Ultimately, it’s on the shop to ask the right follow-up questions when receiving the truck.
“I can’t tell you how many times we’ve gotten ourselves in trouble by just going off of what the driver complaint was on the work order,” said Nate Morris, a technician at Transport Refrigeration. He attributed these to a “misunderstanding between the driver and the service writer.”
Morris, who recently won Thermo King’s inaugural written and skills-based competition for dealer techs, offered an example where a driver told the service writer his APU wouldn’t start, but it started fine in the shop. When pressed for more details, it’s discovered the TriPac unit only failed at certain times of day. Then it’s revealed it only happened when the sleeper was parked at a high altitude. After lifting the hood, Morris said he found a dirty air filter or hung-up injector. That underlying issue combined with the thin air kept the APU from starting.
“That’s why details are everything,” Morris asserted. “This will help get a quick and accurate diagnosis of what’s going on.”
On the other side, DJ Painter, Technician as a Service lead at Noregon, pointed to the importance of training drivers to give the right answers via vehicle inspection reports as well.
“You want your drivers to be just as trained as the technicians—not to turn the wrenches—but to be able to identify an issue,” Painter said.
In addition to road tests to identify “weird wobbles” or other steering-related problems, Orr also advised that drivers have a parts list handy to accurately estimate damage. AdjustRite, PPG’s estimating software solution, has a Shop WorkSheets feature that digitally provides access to a printable parts list via a smart device once VIN is entered, along with labor and paint hours.
“It sounds simple, but a lot of locations that we run across sometimes just use blank sheets of paper, or Excel documents, going off what they see in real life, and then generating a list from that,” said Doug Orr, product manager of AdjustRite.
Having a parts list and “reverse estimating” reduces the need for supplemental additions later, Orr explained, because more internal damage is found at the onset.
“It actually saves you a ton of time when you get back to the office,” he said.
A new AdjustRite tool called Repair Management also lets shops assign work and track hours per repair order through a dashboard. Through this, management can identify who is most efficient at certain repairs based on efficiency and/or focus on training if it’s needed. They can also have a newer tech shadow the more experienced worker to pick up “time-saving tips,” Orr said.
This not only allows shops to complete urgent jobs promptly, but also helps the more raw techs learn how to correctly complete the job the first time. “That’s where that seasoned technician comes in,” said Jeremy Shuey, body and paint shop manager at Housby, a Des Moines, Iowa collision shop. “There are bushings, pivots, and different things that can be missed quite easily.”
Follow the guidance
Making sure mistakes in the shop, like incorrectly torquing wheel-end bolts, don’t lead to an accident on the road is always the number-one priority, but even less sensational repercussions impact both the shop’s and customer’s bottom line.
“Poor repair quality and repair comebacks cost both the vehicle owner and the repairing facility time and money,” noted Robert Braswell, executive director for TMC. “Processes should be in place which reduce or eliminate issues created by human factors.”
As previously noted, those “human factors” are distraction and inexperience—two agents of chaos. Structure and routine, meanwhile, represent order. They are also the building blocks used by OEMs to create repair guidance for specific equipment and components, and at a broader level, used by industry experts to craft TMC’s Recommended Practices. These instructions are born from lengthy discussions by TMC members—including fleets, maintenance providers, and manufacturers—over several meetings. Several hundred are available, and Braswell noted they have been demonstrated to improve repair accuracy and minimize comebacks.
Read more: TMC: VMRS Adapts to Standardize Predictive and Prognostic Maintenance Alerts
One in particular, TMC RP 1604, Rapid Repair Assessment, “provides great guidelines on how fleets and service providers can get to the root of a diagnostic problem within a two-hour window using a field-tested framework for repair success,” Braswell explained. He equated it to the same diagnostic process a medical physician would use to triage an injured patient.
“Following these guidelines—and others like it from TMC such as TMC RP 1609, Quality Control Guidelines—will help achieve faster service, better communication, less downtime, and a friendlier experience each time a driver or customer returns to the maintenance/service facility with equipment complaints,” Braswell added.
Ben Johnson, former director of product management at Mitchell 1, noted that RPs, which are accessible via TruckSeries, are not a “magic bullet,” but can be used as “another piece of information that can be very useful at understanding a specific vehicle configuration and how to diagnose it.”
Because of the rapid pace of technology, more often techs must rely on a tablet in addition to their experience. Noregon customers can access NextStep, an interactive step-by-step guide that offers cautionary tips, while TruckSeries has features such as Advanced Interactive Wiring Diagrams to help techs tackle complicated electrical systems by highlighting the circuits, connectors, and other system elements with access to replacement procedures.
When dealing with ADAS components, Opus IVS’ DriveSafe tool “will prompt users to do the appropriate workflow based on what they’re trying to do in terms of its dynamic or standard calibration,” said Frank Terlep, VP of ADAS (Advanced Driver Assistance Systems) solutions at Opus IVS, a provider of collision diagnostic, estimating, and training tools. On the light vehicle side, a feature called ADAS Map also indicates where ADAS systems are located, what type of calibration is needed, and why.
DriveSafe also includes diagnostic scans assisted by remote experts to further speed up accurate collision repairs.
AdjustRite also uses logic to provide prompts—ranging from just one to potentially 100, Orr said—to guide techs through the repair process and provide reminders based on parts listed in the work estimate.
Following that guidance, whether it comes from the manufacturer, industry-approved materials, diagnostic and repair software, or remote experts like Painter, will not only ensure shops make the correct repairs but do so in an expeditious way while limiting parts expenses.
Quality assurance
The final protection overall will be the road test, but in general, the best prevention against comebacks is solid quality control procedures. Housby has a production manager involved from the start with the vehicle damage analysis, Shuey said, and quality checks are performed during repairs, through the paint shop, and finally before releasing the truck to the customer.
Again, having a structured workflow is crucial. Shuey said making a vehicle blueprint with what’s been repaired and what parts need to be replaced can reduce confusion.
“A lot of people don’t use enough quality control checklists,” Terlep said. “If you’re an airplane mechanic, you live and die by checklists. In our world, they’re not used enough.”
Painter noted it’s also important to check that all tools that need to be calibrated are done so annually, and to red tag those that aren’t. For shared shop tools, tracking is more easily managed. To get techs to stay up to date on personal tools, he suggested offering incentives, like a cash bonus, for staying up to date.
Regular training, whether through OEMs, vendors, or organizations such as ASE or ICAR, can also serve as forms of embedded quality control.
Perhaps most important of all is to use previous comebacks to your advantage by learning from them. While aiming for perfection should be the ultimate target, allowing room for error also provides room to grow.
“There are certain things that you have to learn from failure; you have to right your own wrongs,” Shuey said.
He’s seen managers step in and correct mistakes for their techs, which deprives the tech of that instructive feeling of remorse for messing up.
“If they’re not correcting their own wrong, they’re never gonna learn from it,” he said.
About the Author
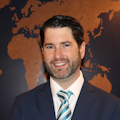
John Hitch
Editor-in-chief, Fleet Maintenance
John Hitch is the award-winning editor-in-chief of Fleet Maintenance, where his mission is to provide maintenance leaders and technicians with the the latest information on tools, strategies, and best practices to keep their fleets' commercial vehicles moving.
He is based out of Cleveland, Ohio, and has worked in the B2B journalism space for more than a decade. Hitch was previously senior editor for FleetOwner and before that was technology editor for IndustryWeek and and managing editor of New Equipment Digest.
Hitch graduated from Kent State University and was editor of the student magazine The Burr in 2009.
The former sonar technician served honorably aboard the fast-attack submarine USS Oklahoma City (SSN-723), where he participated in counter-drug ops, an under-ice expedition, and other missions he's not allowed to talk about for several more decades.