For more on PMs and inspections:
What you'll learn in this story:
- How various fleets track vehicle inspections and maintenance, including through digital platforms
- How to ensure inspections are followed up on and fully passed if there's a defect
While preventative maintenance largely focuses on the vehicles being inspected and repaired, paperwork and recordkeeping play a strong role in making sure fleets are safe and compliant, too. This is especially true given how regimented preventative maintenance (PMs) need to be, with careful logs and schedules set and kept to keep fleets on track.
But as is often the case, there's no one way to track and pass inspections, and which way works best for you may depend on the fleet.
Tracking the trucks
Across the board at all types of fleet service operations, keeping track of and managing inspection activity is deemed equally important.
Dave Forgie, VP of maintenance at Leonard’s Express, reported that on-board telematics systems are used to upload truck mileage and reefer hours multiple times daily, and then reports are sent out via email to each equipment domicile with a shop.
“At NationaLease locations, both basic and component schedules are flagged when a service interval is reached,” said Joe Puff, VP of truck technology & maintenance. “We base this on truck year/make/model, usage, idle time, fuel efficiency, terrain, weather, load type, and duty cycle factors. In other words, even two of the exact same truck can have vastly different inspection schedules if they’re used and driven differently.”
“Penske uses a proprietary system to automatically track and schedule all inspections, including annual inspections,” said Chris Hough, VP of maintenance design and engineering for Penske Truck Leasing. “The scheduling is based on the last completed PM and inspection and the intervals entered when the vehicle was serviced.”
At Lily Transportation, Rusty Stevens, Lily VP of maintenance and fleet services, said the fleet works with vendors to ensure inspection schedules are followed and to receive updates on equipment due.
Jerry Griener, VP of operations, procurement & fleet management at Transervice, noted that the company uses maintenance software to track schedules based on time or mileage. “That data is used to create dashboards and reports to ensure everyone knows what units are coming due,” he added.
“We utilize maintenance management software at Greenbush Logistics that is designed to incorporate alerts,” said Matthew G. Kelly, director of maintenance at Greenbush Logistics.
“Carriers that have maintenance software systems will have alerts set up to notify maintenance supervisors and fleet managers when a vehicle is coming due for a period/annual inspection,” continued Thomas Bray, sr. industry advisor at J. J. Keller & Associates. “At large carriers, that alert will also be built into the fleet dispatch system, so the dispatchers will know when a truck or trailer is due.”
“We use a combination of robust systems and visual checks at Blaine Brothers to ensure nothing is overlooked,” said Blaine Brothers CEO Spencer Dally. “Our ERP system provides automated reminders when inspections are due, keeping us on schedule. At the same time, we rely on visual indicators, such as service and DOT inspection stickers, which our technicians always check when a truck or trailer is in the shop. This dual approach ensures thoroughness and prevents missed inspections.
“Our process also involves technicians using digital tools or physical checklists while working in the service pit or shop,” Dally continued. “These help document and manage inspection activity in real time, ensuring a smooth and efficient workflow. By performing proper inspections throughout the year, we aim to make annual inspections seamless.”
Passing inspections
Blaine’s Dally related that when issues are identified during annual inspections, a structured process ensures timely and effective repairs.
“It begins with the technician compiling a detailed list of deficiencies as soon as the inspection is completed,” he said. “Once the customer decides on the immediate course of action, we proceed with the approved repairs while also scheduling reminders and follow-ups for any deferred work.”
One key point that needs to be understood is that a vehicle cannot pass the inspection if it has a listed defect, Bray advised.
“The technician cannot give the vehicle a ‘provisional’ or ‘conditional’ pass based on the promise that a discovered defect will be corrected in the near future,” he explained further. “If there is such a defect, the vehicle does not pass until the defect is corrected.”
The easiest way to make the grade, though, is to conduct all your PMs—the A’s, B’s, C’s, and down the alphabet—on time and to industry standards. That will make the less common PMs more of a box to check than a moment of truth where you find out what you missed in the past 12 months.
“If proper preventive maintenance is performed consistently throughout the year, there shouldn’t be many surprises during annual inspections,” stated Blaine Brothers Trailer Service Manager Nick Richardson. “Our goal is to ensure that everything is addressed proactively during routine maintenance, so the annual inspection is more of a confirmation than a discovery process.”
About the Author
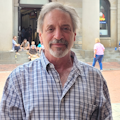
Seth Skydel
Seth Skydel, a veteran industry editor, has more than 36 years of experience in fleet management, trucking, and transportation and logistics publications. Today, in editorial and marketing roles, he writes about fleet, service, and transportation management, vehicle and information technology, and industry trends and issues.