Vehicle alignments present an opportunity for fleets to extend tire life, boost fuel economy, and improve driver satisfaction. While the upfront costs can be significant, the long-term payback can make it a worthwhile investment.
“Alignment equipment can range from a few thousand dollars to around $50,000,” said Ralph Bachemin, senior manager of sales development at Hunter Engineering, a provider of alignment, wheel and tire, and ADAS calibration equipment. “Having the right system for your specific operation makes all the difference.”
Options for setting up service
If a shop plans on performing a lot of alignments, setting up a dedicated bay or service pit could make sense. For shops that anticipate doing just a few alignments a week, a portable alignment system is a good way to go.
“The alignment system we’ve put together can be rolled around our shops,” said Daniel Mustafa, director of technical service at TravelCenters of America, which employs nearly 3,000 technicians at its TA Truck Service Centers across the country. “Our system includes a stand with a computer and printer. All of the sensors and remote-control connections can be stored in the rear of that stand. There is plenty of mobility. We typically store our system in a cage when a technician isn’t using it. The price on any computerized alignment system is rather high, so you definitely want to protect it.”
Also in the interest of mobility, TA Truck Service refrains from utilizing lifts or platforms. Alignments are performed with the vehicle parked on the ground. “You just drive the front wheels onto turn plates to eliminate any friction from the scrub of the tire on the ground,” Mustafa explained. “If you have the brakes released so the vehicle can roll a bit, the thrust angle can be adjusted without the need for any other specialized equipment.”
For a shop going that route, turn plates are a separate investment. A rack would require additional investment, too, but the time savings and other benefits could more than offset it over time—particularly for a shop performing alignments on a regular basis.“Our setup uses an alignment rack that gets the truck to a height where adjustments can be made from a standing position,” said Tim Lamoreaux, truck service manager at North American Trailer in Inver Grove Heights, Minnesota. North American Trailer is a subsidiary of Blaine Brothers, which provides parts, service, and towing in Minnesota and Wisconsin. Lamoreaux has also worked at Blaine’s TruckAline business. “The racks are set up in two-foot sections so you can remove a section to gain better access to the suspension. This setup prevents a lot of the up-and-down work that can lead to back and leg strains,” he said.
Hunter’s Bachemin said he is starting to see more shops look to some type of rack or lift to help perform alignments. “I conducted a time study and found that the time saved while using a rack is about 25%. Using a rack requires a lot less effort. Suspension parts are often pretty tight and require a cheater bar to get them loose. There isn’t much room for leverage when the vehicle is not up in the air,” he explained.
Benefits of a computerized system
When it comes to the alignment equipment itself, shops can choose between a manual and computerized system. While both ultimately perform the same task, the effort required—and end result—may differ greatly.
“With a manual system, the technician needs to be capturing measurements with mechanical gauges and writing all of that information down,” said Chris Schutt, technical training specialist at Bee Line, a manufacturer of computer laser wheel alignment, tire balancing, and frame correction equipment. “Manual and computerized alignments are both simple, really. But a computerized system is much faster and easier to teach.”
“A computerized system walks the technician through the process,” added Lee McLaughlin, Bee Line owner and president. “That makes it easier to cross-train technicians. Our system has help screens and videos that guide the technician through the process.”
Hunter’s computerized system offers two levels of software. One has additional functionality that walks a technician through the alignment process. The other level is more self-guided, making it a more cost-effective option for a technician who is already somewhat familiar with performing alignments.
TA Truck Service has stuck with the same computerized alignment system for many years. In fact, Mustafa first learned how to perform alignments on this system several years ago. Additionally, TA has begun experimenting with a second system. As Mustafa pointed out, all systems have their pluses and minuses.
“The new system we’ve been testing has another level of mobility in that we can load it onto a service truck,” he continued. “It can work effectively anywhere. On the other hand, the system we’ve been using for years, while very accurate and reliable, can have some issues on really sunny days because the light can throw off the lasers. Because it uses a different technology, the new system we’ve been testing doesn’t seem to have that issue.”
Equipment and tooling needs
Aside from the alignment system itself, and perhaps some turn plates or a rack, the typical maintenance shop will already have much of what it needs to begin doing alignments. Mustafa said the typical technician can get everything else they need for less than $500.
“The first thing a technician needs is something to turn the tie rod,” he said. “That might be something like a four-foot pipe wrench. The technician will also need something to manipulate the positioning of the rear axle, likely some kind of hydraulic tool.”
Hunter’s Bachemin said a shop will also want to keep plenty of alignment shims in its parts inventory for when technicians are making the actual adjustments.It’s a good idea to ensure that the alignment system itself will allow for a complete alignment. Bee Line is a big believer in what it refers to as “total vehicle wheel alignment.”
“You’re not just aligning wheels to wheels, which is considered a thrust angle alignment,” McLaughlin said. “You’re actually aligning the axles 90-degrees parallel to the centerline of the frame so the entire truck goes down the road straight.”
Some alignment systems may only measure and adjust toe and tracking errors. Total vehicle alignment requires all critical angles to be gauged, and both camber and caster to be corrected. Fleets should ensure that the system they invest in has the tooling and capabilities to address all critical angles.
Additionally, Bachemin said it’s beneficial to have a system that can measure all three axles simultaneously, which makes things easier on the technician while boosting efficiency.
Recognizing the importance of a three-axle alignment is critical. “If the truck has a pull, it doesn’t necessarily mean there is anything wrong with the caster and toe,” North American Trailer’s Lamoreaux explained. “The drive axles could just as easily be pushing the truck left or right.”
Training and support
Like with any specialized service, technicians are going to need some training to get up and running with alignments. Equipment manufacturers often provide a combination of online video training and in-person training at their facilities. Additionally, many will send trainers to a shop that recently invested in their equipment. As a general rule, the training often lasts one to three days depending on the experience level of the technicians.
At TruckAline, a new technician is trained for at least four weeks with a senior alignment technician before being sent on their own. And even then, close supervision continues to take place for some time.
“It’s one thing to know that adding caster to the right side will help correct a right pull, but knowing how much to add without causing a left pull and premature tire wear takes time and experience,” Lamoreaux said. “The alignment equipment we use is fairly straightforward and the computer makes recommendations, but it’s all about feel. It’s also important to test drive the vehicle to see if any improvements were made, so having a CDL is a huge advantage for an alignment tech.”
Maintaining the accuracy of an alignment system does require some regular maintenance, primarily cleaning and lubing certain areas. System calibration is also important. Calibration can be affected by several things, including extreme weather and humidity. Additionally, a technician can sometimes drop a sensor onto the ground.
“Having the calibration checked at least a couple of times a year is nice,” Hunter’s Bachemin said. “It’s even better when technicians can check it themselves without having to call out a service professional. The actual calibration procedure does require special tools. But a technician can check to make sure the system is calibrated on their own. We have a reverse sensor test that takes five to seven minutes. Anytime a technician drops a sensor or is seeing data that just doesn’t seem right, it’s a good idea to run this test to put their mind at ease.”
McLaughlin said Bee Line’s system allows technicians to perform the actual calibration themselves. “We write our own software, and calibration is built right into the cabinet itself,” McLaughlin pointed out. “This allows the technician to calibrate in roughly four minutes.”
When a fleet decides to venture into alignment services, Bachemin said it must be an all-in commitment. There is good reason to make that commitment. Technicians can get up to speed and develop some proficiency fairly quickly, especially with a computerized system. Alignments also present a good money-making opportunity.
“In the heavy-duty world, it’s realistic to say that 80% of the vehicles out on the road are in need of an alignment,” Bachemin said. “Checking alignment every 25,000 miles could help a fleet save 2-4% on fuel and up to 20% [on] tire life. That is money to a fleet.”
And for the shop, the money is in providing a valuable service that helps fleets save over the long haul.
Automating alignment checks
Hunter has recently introduced a newer product that can help a fleet stay on top of alignments.
Quick Check Commercial consists of two systems that can be purchased together or individually. As a vehicle drives into a service area, Quick Check Heavy Duty uses cameras and lasers to check alignment on the steering axle and scrub angle on the two rear axles as well as scrub angle on the trailer. The other element of the Quick Check Commercial system is Quick Tread Heavy. It also uses cameras and lasers to measure tread depth on all 18 tires.
“Essentially, the alignment can be checked in the time it takes to drive 100 feet,” said Ralph Bachemin, senior manager of sales development at Hunter Engineering, a provider of alignment, wheel and tire, and ADAS calibration equipment. “The data is reported through an internet-based system. Then the fleet manager can see when a certain vehicle or trailer is in need of some alignment attention.”
About the Author
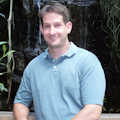