Fuel-operated heaters have been around for decades, but it’s surprising how little many maintenance professionals know about them and the benefits they provide. Let’s change that right now with a pop quiz.
First, here’s a simple question. Which runs dirtier: a cold or warm diesel engine? Of course, you know that a cold diesel engine puts out a lot more soot and particulate matter. Folks always answer that correctly when I ask.
Here’s another. Which uses more fuel and puts out more emissions: a big diesel engine or a tiny fuel-operated heater? The big one, obviously, as the heater burns relatively very little fuel, and thus a small fraction of the engine’s emissions output. Most get this one right as well.
How about a tougher math question: How much does your fleet spend annually on DPF cleaning? If you’re anything like 87% of the maintenance professionals surveyed in a recent fleet study conducted by Webasto—in conjunction with Fleet Maintenance—you don’t know the answer to this very important question. You probably should.
And how much does your fleet spend annually to replace damaged and inoperable DPFs? According to the survey, 65% drew a blank on this question as well.
Finally, do you have any idea how many hours longhaul trucks spend idling each year and what percentage of a vehicle’s running time this represents? According to the U.S. Department of Energy, a longhaul truck idles about 1,800 hours per year, and uses about 1,500 gallons of fuel to do so. And industry experts suggest that it’s not unusual for idling time to represent as much as 45 to 50% of a vehicle’s running time. Don’t feel bad if you didn’t know the answer to this one either, most maintenance folks don’t.The down and dirty on DPFs
Let’s start with some very basic, but important, facts. Until an engine is operating at between 842 to 1,112 degrees F, which is common at road speeds and well above idling temperature, the DPF is essentially used as a ‘garbage can’ for the collection of soot and PM. The DPF is a temperature-dependent device, so without sufficient exhaust operating temperatures, the lifespan of every DPF will be negatively impacted by lower operating temperatures.
Cold starting or idling a diesel engine basically turns it into a soot- and smoke-generating machine that feeds directly into the DPF. The combination of un-combusted fuel and PM create a heavy, wet, and dense coating that forms on the surface of the DPF. The contaminants increase backpressure, resulting in significant reductions in engine and DPF efficiency. Face plugging and filter overload are generally the byproducts. Cold starts also create the need for more frequent DPF cleanings, which cost fleets time and money, while shortening a DPF’s effectiveness and its lifespan.
Temperature-related issues can also occur in vehicles with short duty cycles, such as last-mile delivery. Frequent throttle-on and -off sequences create the same type of sub-optimal temperature and increased emissions environment. The DPF’s catalyst can’t maintain regeneration temperatures and the DPF becomes overloaded, and plugging can result.
If one factors in downtime for DPF cleaning and replacement, costs can range between $2,500 to $8,000 per vehicle. It also adds up to a lot of extra work for fleet maintenance folks–work that could otherwise have been avoided.
As one fleet professional put it: “If you can reduce the crud that’s coming out of the stack before it goes into the DPF, you’ve just won half the battle right there.”
Needless to say, I agree.
Pre-conditioning prevents DPF problems
But how do you win the battle? The economical solution is to pre-heat or pre-condition a diesel engine using a fuel-operated heater. These compact devices warm the engine and its fluids to about 160 degrees F and keeps it there until the engine is started. These devices operate on diesel fuel drawn directly from the vehicle’s primary fuel tank.
Common solutions, such as the Webasto Thermo Top Evo coolant heater, have been proven to reduce cold dense soot by up to 66% during engine startups and reduce NOx emissions by up to 40% (which was tested by an independent lab according to TMC recommended practices 432A and 1102).
By raising the initial engine temperature at startup, FOHs can also help shorten the time it takes for the DPF to become active, reducing the “wet stacking” often produced by cold engine starts and significantly increasing the time between cleaning intervals.
When operators start a pre-heated engine, they also immediately get warm air from the HVAC system, so they don’t have to wait for the engine to warm up. Coolant heaters and fuel-operated bunk heaters can also be controlled manually or through the use of Bluetooth-enabled controllers.
By pre-heating the engine block, oil is warmer, piston rings remain sealed, and engine blow-by is diminished. The amount of carryover oil in the exhaust stream is also reduced. Warmer injectors mean increased fuel efficiency, and DPF tanks and injectors won’t freeze in cold climates. However, one of the most important advantages of pre-heating is reduced maintenance costs on DPFs and the rest of the aftertreatment system.
Outside of the initial purchase and installation cost, these heaters only require about a half cup of fuel per-hour to operate. If a gallon of diesel costs roughly $5, then this equates to about $0.16.
So, the final question I have is this: how much is reducing DPF issues worth to your fleet?
About the Author
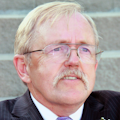
Duane Bratvold
Western Regional Sales Manager, Customized Solutions, Americas Region, Webasto Group
Duane Bratvold serves as Western regional sales manager, customized solutions, Americas Region for Webasto Group. Bratvold uses his expertise in emissions standards to provide FOH and other emissions management solutions for fleets of trucks, buses and off-highway equipment.
In his capacity, Bratvold also serves as Webasto’s corporate expert on emissions and is respected within the commercial vehicle industry for his vast knowledge and 40 years of experience within the diesel emissions sector. Over his career, he has worked in partnership with many state and federal municipalities on emissions and retrofit initiatives. Bratvold has also worked with DPF and engine manufacturers, giving him a unique understanding of the effectiveness of emission control devices and their many applications.