Fleets spend a lot of time and money trying to get more life out of their tires. But according to John Ashal, president of Big Rig Alignment Co., many fleets are missing the one essential ingredient in a holistic tire management program: alignments.
“A high-performing tire is not only properly mounted and inflated, but also properly balanced,” Ashal explained. “Furthermore, a high-performing tire must be centered on the hub of a mechanically sound, properly aligned vehicle.” Big Rig Alignment specializes in OEM factory alignment programs.
It’s not just tire wear that fleets should be concerned about.
“Wheel alignment affects a multitude of vehicle characteristics,” said Doug Felt, technical training manager for Hunter Engineering, a manufacturer of heavy-duty vehicle alignment equipment, wheel service equipment, and other products. In addition to premature tire wear, Felt points to:
- Fuel economy
- Directional stability
- Braking performance
- Cornering
- Steering effort
- Ride quality
While some of those characteristics impact the bottom line, some also affect the driver.
“Constantly fighting the vehicle’s tendency to leave the intended path will fatigue a driver quickly,” Felt pointed out. “Poor ride quality makes for an uncomfortable trip.”
Don’t forget about safety, which is compromised when braking performance is less than designed and/or the vehicle is constantly moving to the left or right of the intended path.
Regular alignment checks can help keep Compliance, Safety, Accountability (CSA) scores lower by reducing a fleet’s exposure to out-of-service violations and associated vehicle downtime.
“Infractions relating to tires, wheels, suspensions, steering mechanisms, frames, and driveline components can often be avoided by identifying problems during alignment checks,” said Chris Schutt, technical training specialist for Bee Line Co., a manufacturer of computer laser wheel alignment, tire balancing, and frame correction equipment.
“An improperly aligned vehicle is placing additional stress on suspension and steering components,” Felt added. “Premature failure of kingpins, wheel bearings, and tie rod ends is common.”
As noted, there are numerous reasons why a fleet should take alignments seriously. The reason why many don’t, however, is because an alignment sometimes isn’t the remedy to a problem a vehicle is having. Alignments need to be performed correctly at the right times.
“As we go out and look at tires in the field, only 50% of the irregular wear on steer axle tires is due to an alignment problem,” said Mike Beckett, president of MD Alignment Services, a provider of alignment equipment, training, and consulting services. “That means half of the steer axle problems are the result of other causes. On drive and trailer tires, less than 10% of the tire wear problems result from misalignment. If a fleet is just sending trucks in to get alignments to fix all of their tire problems, the odds are that they won’t be happy.”
Warning signs of a bad alignment
Beckett has personally been performing heavy-duty alignments for roughly 50 years. He said there are a handful of common causes of irregular tire wear that are not alignment related. “The ability to identify the tire-wear pattern before taking any corrective action is the most important part of the diagnostic,” Beckett said.
Technology & Maintenance Council (TMC) Recommended Practice (RP) 642 has a section on tire wear identification. The RP explains how wear patterns such as cupping and diagonal wear are indications of a non-alignment problem. Possible signs of an alignment issue are rapid shoulder wear and one-sided wear. The biggest indicator is feathering.
“Feathering occurs when you slide a tire sideways,” Beckett explained. “That’s why feathered wear always indicates an alignment problem, whether there’s feathering on one front tire or both of them. Drivers and technicians should regularly check for feathered wear.”
TMC RP 642 explains that if the steer tires have feathered wear in opposite directions, the problem is likely a toe condition that could be remedied per the guidelines in TMC RP 219. However, if the feathered wear goes in the same direction on both steer tires, there is a definite alignment issue to correct. Or, if one steer tire shows normal wear but the other is feathered, it could be a combination of toe issue and misalignment. Beckett’s advice is very simple: “If you feel feathered wear at all, get an alignment done.”
“A simple, quick check for feathering can be done during the pre-trip inspection,” Big Rig Equipment’s Ashal added. “The driver can run their hand across the steer tires. If it feels smooth in one direction but rough in the other direction, there is some feathering going on. There’s also a good chance that some rubber has worn off. The vehicle is also starting to pull a little, typically to the right. An experienced driver is going to notice that right away and should let the fleet manager know.”
Hunter Engineering’s Felt says technicians can also help keep an eye out for feathered wear. Additionally, there are some other signs of improper wheel alignment to look for.
“Technicians should inspect all tires for signs of excessive camber wear which occurs gradually,” Felt recommended. “Front wheels are more likely to have excessive camber angles. Excessive camber causes more load to be placed on the shoulder of the tire, causing the shoulder to get hotter. The result is a smooth wear pattern near the shoulder of the tire.”
Setting up an in-house alignment program
If a fleet decides to bring its alignment services in-house, Ashal says there has to be a strong commitment and even stronger accountability.
“A fleet shouldn’t just buy an alignment machine and stick it in the corner of the shop,” he said. “A fleet also shouldn’t treat alignments like a lube service where anybody does it if they have some free time. It’s helpful to have a dedicated technician who’s responsible for alignments. This person should be well-trained. Then he or she will become an expert and also develop a good routine that helps with quality and consistency.”
Investing in the right alignment equipment is equally important. There are numerous options out there ranging from around $1,000 to literally tens of thousands of dollars. When choosing the best option for its shop, a fleet needs to keep a few things in mind: usability, accuracy, and return on investment (ROI).
According to Ashal, very few alignment machines are truly repeatable. That is why he advises a fleet to ask an equipment provider for independent testing numbers before deciding on a purchase. “At the very least, the equipment manufacturer should be willing to demonstrate the repeatability of their equipment,” Ashal added.
Once a piece of alignment equipment is in the shop, a technician needs to make sure it is calibrated on a regular schedule to ensure precision.
MD Alignment’s Beckett says the frequency of calibration will vary slightly from one piece of alignment equipment to the next, as well as how often the machine is being used. That said, the tests Beckett helped conduct as part of the TMC Task Force on alignment equipment found that the typical computerized alignment machine needs to be calibrated roughly every 20 cycles.
“If the alignment equipment is off every time you check it at 20 cycles, you better start checking it more frequently,” Beckett said. “You may also have to find out if something is wrong with your machine that is causing it to drop out of calibration.”
Speaking of calibrations, Bee Line’s Technical Training Specialist, Chris Schutt, said fleets should look for alignment equipment that is user-friendly and easy for technicians to calibrate themselves. “If you have an alignment unit in your shop that can’t be self-calibrated, you’re going to experience downtime while you wait for service,” Schutt pointed out.
Best practices for heavy-duty alignments
Sometimes calibration isn’t the problem. Sometimes a technician isn’t following proper alignment procedures.
“That is operator error, and we typically find that it is due to inadequate training,” Beckett pointed out, adding that a technician who can perform brake jobs needs about a day’s worth of good alignment training.
Another possible cause of improper alignment is the fact that the technician is using factory specifications. The problem with that, Beckett explained, is that those factory specs are based on getting a truck through the assembly line in a certain amount of time. In a real-life setting, however, a fleet needs a much tighter tolerance when it puts the truck out on the road.
“Over the years, we have created a ‘performance’ spec,” Beckett said. “Our numbers are always within the factory build spec, but are nowhere near as broad.”
Fleets should also think about how much an alignment might change during a vehicle’s initial delivery from the factory to the fleet.
“We’ve found that up to 50% of vehicles see a significant change in alignment,” Beckett said. That’s why an initial alignment check is important once the fleet takes delivery of a new vehicle. Then, another check is often necessary within the first 30 days of operation because the vehicle’s parts are settling in line. This is where drivers and technicians can monitor for feathered wear on the steer tires.
“We like to check trucks again at 60 days, only now there is a considerably lower probability that a truck needs adjusting,” Beckett said. “By the time we do a 90-day check, almost all have quit changing.”
That is why TMC RP 642 recommends checking alignment after an initial break-in period of 15,000 to 30,000 miles, or no more than 90 days. Technicians are advised to inspect tire/wheel assemblies for tire wear. An all-axle alignment is also recommended after this break-in period. Then, an all-axle alignment is recommended every 80,000 to 100,000 miles, or 12 to 18 months.
Bee Line’s Schutt said fleets should design preventive maintenance (PM) programs and schedule PM intervals based on the fleet’s unique vehicle types, the environments they work in, and the duty cycle severity their vehicles are exposed to. “No two fleets are exactly the same, nor is there a one-size-fits-all alignment program that will meet everyone’s needs,” Schutt pointed out.
According to Schutt, light-duty and in-town commercial vehicles should have an alignment performed about every six months. This includes vehicles engaged in the growing last-mile delivery service segment. At the other end of the spectrum, heavy-duty long-haul vehicles should be scheduled for alignment service at least once annually.
Vocational vehicles create a different scenario. Schutt said alignment needs can vary greatly depending on the severity of the terrain and duty cycle intensity. “A good rule of thumb is that the more demanding the operating environment, the more often an alignment should be performed,” he noted.
Hunter Engineering’s Felt said it’s important to examine the various factors that may cause wheel alignment to change.
Road conditions. Highway surfaces are relatively easy on heavy-duty vehicles since they are relatively smooth with no sharp turns. Two-lane blacktop roads, on the other hand, may be less smooth and require more turning on the front wheels. “The pitch of the road may also require the driver to maintain steering effort,” Felt said. Then, city roads present a mixed bag of surface types, sharp turns, and defects. Gravel roads are inherently hard on suspension and steering components.
Ride height (spring height) changes. A vehicle carrying heavy loads will have ride height changes before a vehicle carrying light loads. Those changes may occur rapidly if a vehicle is loaded to capacity.
Road defects. Potholes, bumps, and dips often stress the suspension and steering components, causing alignment angles to change.
“Vehicles used in harsh conditions will require frequent wheel alignments,” Felt said. “Vehicles driven primarily on highways may need wheel alignment once or twice a year. The best advice is to have the wheel alignment checked often—because one never knows when changes to suspension and steering components occur.”
Aside from establishing proper routines for break-in alignment checks, tire wear inspections, and alignment equipment calibrations, fleets need to know how a proper alignment is performed. Alignment equipment manufacturers typically provide excellent training, as do associations and companies like MD Alignment Services. Big Rig Alignment works with OEs and dealerships.
Alignment services can either help fleets save money on tires or simply become another operating expense. It all depends on whether or not an alignment is what is actually needed, and whether or not the fleet is willing to commit to accuracy. When all of those factors are in alignment, bringing alignment services in-house can be a really wise investment.
All-axle alignment checklist
TMC RP 642 includes an all-axle alignment checklist for technicians to follow:
- Check tire inflation pressure
- Road test vehicle to determine vehicle-handling dynamics
- Check steering, suspension, and frame components, as well as axles
- Check brake drum centering
- Check wheel bearing endplay
- Check wheel/tire runout
- Check tire mounting
- Inspect tires for irregular or unusually fast wear
- Check vehicle ride height
- Check steer axle spindle height
- Position vehicle in the shop’s alignment area by driving straight ahead with minimal use of brake and throttle
- The alignment area should be flat and level, or at least where a known value can be compensated for
- Measure and record alignment parameters
- Road test vehicle
About the Author
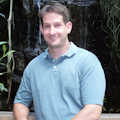