Wheel end bearing adjustment is often viewed as an isolated task that will only determine if the bearings will wear reasonably well and not fail prematurely. However, the procedures used, and the final settings that result, in wheel end bearing adjustments have a big impact on the efficiency and cost of maintenance as well as every facet of the wheel end performance of tractors and trailers.
Endplay or no endplay
The majority of Class 8 wheel ends are referred to as conventional wheel ends, or manually adjusted wheel ends. Technicians use torque wrenches to turn a spindle nut and apply torque force to the nut, which then applies an unknown amount of load force to the bearings. The last steps call for a “turn back” of the spindle nut, which can leave bearings “loose” in an endplay setting. A dial indicator is supposed to be used to measure how much endplay is in each and every wheel end after it is adjusted.
Alternative wheel end systems, referred to as “pre-adjusted,” often result in bearings set to endplay and cannot be further adjusted to improved settings.
Endplay bearing settings compromise bearing and wheel end performance. Bearing manufacturers state the best bearing life occurs when all endplay is removed, and bearings are set to light preload.
The Society of Automotive Engineers (SAE) published Surface Vehicle Recommended Practice J2535 as a guide that shows optimum life at preload settings ranging from 250 to 500 ft-lbs for steer axles and 500 to 1,000 ft-lbs for drive and trailer axles.
Innovations over the past 10 years now enable fleets to remove all endplay from their wheel ends, set the bearings to the SAE light preload settings and enjoy all the benefits of better performing wheel ends.
Consistency, speed and accuracy
There are three key aspects for maintenance managers to consider with their wheel end bearing adjustment process:
- Consistency
By their nature, torque wrench procedures can be very difficult to control. This is true for a single technician, but it becomes nearly impossible to maintain consistent practices from technician to technician, and from shop to shop. Even with frequent wheel end training, torque wrench procedures leave a lot of room for each technician to make small adjustments to create their own process. The spindle nut “turn back” step alone introduces wide variability in the final setting. Maintenance managers express great frustration with this lack of consistency in their wheel end maintenance, because they know it results in costly wheel end performance issues.
- Speed
Maintenance organizations are constantly reviewing their operations for efficiency improvements so they can invest their technicians’ time wisely. Current torque wrench procedures are slow and cumbersome, and consume too much valuable technician time to achieve poor results.
- Accuracy
A fine human hair has a diameter in the range of 0.003” to 0.005”. For some time now, the recommended endplay settings for wheel bearings is 0.001” to 0.005” of looseness. Most field engineers confirm wheel end bearings to be in a range from 0.003” to over 0.010”. Just a small twitch of the torque wrench during the “turn back” step certainly can change the setting by much more than the diameter of a human hair.
The benefits of eliminating endplay
Engineers and technical experts agree optimal wheel end performance and safety can be achieved when all endplay is eliminated, and the bearings are set to light preload.
- Improved bearing life
Without endplay, bearings last longer because more of the tapered rollers share the vehicle load. When loose, the load is not well distributed and can cause premature wear and other issues within the bearings.
- Reduced seal failures
Wheel seals that leak are blamed on seal quality, incorrect installation and other environmental conditions. Loose bearing settings directly impact seal function, and will lead to wear and tear, and quick premature failure.
Fleets that remove endplay from their bearings report seal failures have been eliminated. This translates to reduced maintenance costs, reduced warranty claims and a decrease in technician labor time handling seal failures.
- Lower tire program costs
Most fleets suffer from some degree of uneven tire wear, leading to low tire removal mileage. Causes of low tire mileage, sometimes severe, may include alignment problems, poor tire balancing, under-or over-inflation, and service duty of the vehicles.
Improper bearing adjustment is almost never mentioned by maintenance staff as a cause of uneven tire wear and premature tire removal. Yet, no less than 14 different uneven tire wear problems listed in the Technology and Maintenance Council’s Radial Tire Conditions Guide are attributed to improper bearing adjustment (too much endplay).
Fleet maintenance managers who implement a program to eliminate endplay from wheel ends report a rise in their tire removal mileage. This translates directly to lower tire program costs.
In addition, other wheel end problems, including brake system performance, ABS faults, steering vibration and overall ride quality all can be caused by loose wheel end bearings.
Maintenance managers who experience one or more of the wheel end performance problems listed above should consider the possibility their bearing adjustment procedures may be the culprit.
John E. Rode founded Temper Corporation in 1969, and has been engineering solutions and manufacturing bearing adjustment products for industrial and commercial vehicle bearing assemblies. He founded Temper Axle Products Corporation in 2006 to make and distribute Doctor Preload bearing adjustment tools and Temper-Loc spindle nuts. John is a mechanical engineer, BSME Iowa State University, 1959 and MSME University of New Mexico, 1961. He is the inventor of record on more than 100 U.S. and foreign patents and was named Entrepreneur of the Year in New York State in 2001.
About the Author
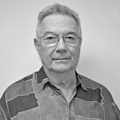
John E. Rode
Chief Executive Officer, Temper Companies
John E. Rode founded Temper Corporation in 1969, and has been engineering solutions and manufacturing bearing adjustment products for industrial and commercial vehicle bearing assemblies. He founded Temper Axle Products Corporation in 2006 to make and distribute Temper EMT (Endplay Measuring Tool) with special wrenches for adjusting wheel end bearings to TMC recommended endplay settings, and Doctor Preload bearing adjustment tools for setting SAE recommended preloads, along with Temper-Loc premium single nut spindle nuts. Rode, a mechanical engineer, has a BSME from Iowa State University and an MSME from the University of New Mexico. He is the inventor of record on more than 100 U.S. and foreign patents, and was named Entrepreneur of the Year in New York State in 2001.?